[Precision ERW tube mill machinery]Exploring the Advancements and Applications of Precision ERW Tube Mill Machinery in Modern Manufacturing Industries
News 2024-12-5
In the fast-evolving landscape of manufacturing, where efficiency and precision are paramount, Precision Electric Resistance Welded (ERW) tube mill machinery has emerged as a critical component for various industrial applications. This advanced machinery enables manufacturers to produce high-quality welded tubes and pipes, crucial for sectors ranging from construction to automotive and beyond. In this article, we will delve into the workings, advantages, and applications of Precision ERW tube mill machinery, highlighting its impact on modern manufacturing processes.
**Understanding ERW Tube Mill Machinery**
At its core, ERW tube mill machinery operates on the principle of electric resistance welding, a process that utilizes electrical resistance to heat the edges of flat metal strips until they reach a molten state, allowing them to be fused together. The machinery consists of several stages, including strip preparation, forming, welding, sizing, and finishing. Each of these stages is meticulously designed to ensure high precision and uniform quality throughout the production process.
**Key Components of ERW Tube Mill Machinery**
1. **Strip Preparation Stage**: This initial stage involves cleaning and aligning the metal strip, typically made of carbon steel or stainless steel. This ensures optimal welding conditions, free from contaminants that may affect the integrity of the weld.
2. **Forming Section**: The prepared metal strip is then fed into a series of rollers that shape it into a cylindrical form. This forming process is critical as it dictates the final geometry and dimensions of the tube being produced.
3. **Welding Station**: This is where the actual electric resistance welding occurs. The edges of the formed strip come together, and an electrical current is applied, causing the material to heat and bond. The precision of this stage is crucial, as it directly influences the strength and quality of the final product.
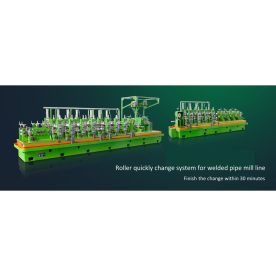
Exploring the Advancements and Applications of Precision ERW Tube Mill Machinery in Modern Manufacturing Industries
5. **Finishing Operations**: The final processes may include cutting, straightening, and surface treatments, tailored to meet specific requirements for different applications.

Exploring the Advancements and Applications of Precision ERW Tube Mill Machinery in Modern Manufacturing Industries
One of the primary advantages of Precision ERW tube mill machinery is its ability to produce tubes with consistent quality and precise dimensions. This is particularly important in industries like construction, where structural integrity relies heavily on material quality. Furthermore, the efficiency of the ERW process allows for high-speed production, enabling manufacturers to meet growing demands without compromising on quality.
Another significant benefit is the versatility of the machinery. Precision ERW tube mills can be adapted to produce a wide range of tube sizes and thicknesses, accommodating diverse client specifications and industry standards. Additionally, modern ERW mills often feature automation technology, which streamlines operations and reduces the need for manual intervention, further enhancing efficiency and reducing labor costs.
**Applications of Precision ERW Tube Mill Machinery**
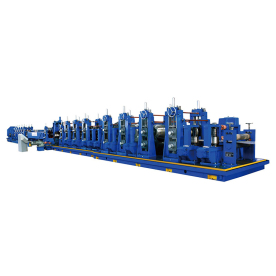
Exploring the Advancements and Applications of Precision ERW Tube Mill Machinery in Modern Manufacturing Industries
Moreover, the energy sector relies on ERW tubes for pipelines and casing in oil and gas extraction, where the durability and pressure resistance of the tube are paramount. Other industries that benefit from precision ERW tube manufacturing include furniture, home appliances, and telecommunications, each requiring tailored specifications to meet specific needs.
**Conclusion**
Precision ERW tube mill machinery represents a significant advancement in the manufacturing landscape, offering unparalleled quality and efficiency in tube production. As industries continue to demand higher standards and faster production rates, the role of ERW technology becomes increasingly vital. By understanding the workings, advantages, and applications of this machinery, manufacturers can position themselves for success in an ever-competitive marketplace, ensuring they meet the demands of their customers while maintaining the highest quality standards. As technology continues to evolve, it will be exciting to see how Precision ERW tube mill machinery adapts and grows, driving innovation in the manufacturing sector for years to come.