[Precision induction heating equipment]Exploring the Advantages and Applications of Precision Induction Heating Equipment in Modern Manufacturing Processes
News 2024-12-5
****Induction heating has revolutionized the way industries approach heating applications, leading to significant improvements in efficiency, precision, and energy consumption. Among the various technologies available, precision induction heating equipment stands out for its unparalleled performance in a wide range of applications. This article delves into the workings, benefits, and diverse uses of precision induction heating equipment in modern manufacturing processes.
What is Precision Induction Heating?
Precision induction heating is a process that utilizes electromagnetic fields to generate heat in conductive materials, typically metals. By employing high-frequency alternating current in a coil, a magnetic field is created, which induces electrical currents within the workpiece. This phenomenon, known as eddy currents, generates heat due to the electrical resistance of the material. The primary distinction between traditional heating methods and precision induction heating lies in the targeted, localized heating it provides, allowing for greater control over the process and superior results.
Advantages of Precision Induction Heating Equipment
1. **Energy Efficiency**: One of the most significant benefits of precision induction heating equipment is its energy efficiency. The heating occurs directly in the material, minimizing energy loss to the surroundings. This efficiency translates into lower operational costs and reduced environmental impact.
2. **Speed**: Induction heating is known for its rapid heating capabilities. The equipment can achieve high temperatures in a matter of seconds, which is drastically faster than conventional heating methods such as furnaces or gas heaters. This swift response time helps manufacturers meet tight production deadlines.
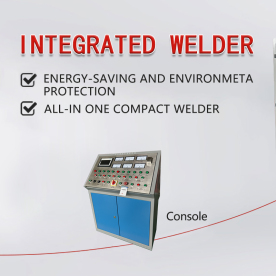
Exploring the Advantages and Applications of Precision Induction Heating Equipment in Modern Manufacturing Processes
4. **Non-Contact Heating**: The non-contact nature of induction heating reduces the risk of contamination or oxidation of materials. It also minimizes wear and tear on equipment since no direct flames or heated surfaces are involved.
5. **Versatility**: Precision induction heating equipment is adaptable and can be used across various industries for multiple applications. From metal forming and welding to heat treating and bending, the equipment is versatile enough to handle different heating tasks.
Applications of Precision Induction Heating Equipment
Given its numerous advantages, precision induction heating equipment is employed in various sectors, including:
- **Manufacturing**: In the manufacturing sector, precision induction heating is extensively used for processes such as metal hardening, annealing, and forming. The ability to focus heat precisely at specific points allows manufacturers to achieve enhanced material properties and performance.
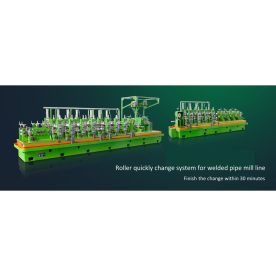
Exploring the Advantages and Applications of Precision Induction Heating Equipment in Modern Manufacturing Processes

Exploring the Advantages and Applications of Precision Induction Heating Equipment in Modern Manufacturing Processes
- **Aerospace**: Precision induction heating equipment is crucial in the aerospace sector, where high standards for quality and safety are required. It's employed for brazing critical components and heat treatment of alloys, contributing to the overall reliability and performance of aircraft parts.
- **Jewelry Making**: Artisans in the jewelry industry use precision induction heating for soldering and metal forming. The precise control offered by induction heating ensures that delicate materials are not damaged during the heating process.
- **Oil and Gas**: Pipe welding and heat treatment processes in the oil and gas industry often utilize precision induction heating equipment due to its ability to achieve highly localized heating, improving joint integrity and lifespan.
Conclusion
Precision induction heating equipment is essential in modern manufacturing, offering numerous advantages over traditional heating methods. Its energy efficiency, speed, and precision make it an invaluable tool across various industries, from automotive and aerospace to jewelry making and oil and gas. As technology continues to advance, the role of precision induction heating is expected to expand, further enhancing production methods and fostering innovations in the manufacturing sector. Investing in this technology not only improves operational efficiency but also contributes to better quality control and product outcomes.