[Pipe mill production line with quality control measures]An In-Depth Exploration of Pipe Mill Production Line with Emphasis on Quality Control Measures for Enhanced Operational Efficiency
News 2024-12-4
****The pipe mill production line is a vital component in the manufacturing sector, with its processes directly influencing the quality and reliability of pipes produced for various applications. As industries continue to demand higher standards for performance, safety, and durability, the importance of integrating comprehensive quality control measures into the pipe mill production line cannot be overstated. In this article, we will examine key aspects of the pipe mill production line, the role of quality control measures, and how these protocols enhance overall operational efficiency.
**Understanding the Pipe Mill Production Line**
The pipe mill production line typically encompasses several processes, including raw material selection, forming, welding, sizing, heat treatment, and finishing. Each stage of production is integral to ensuring that the final product meets the necessary specifications and standards.
1. **Raw Material Selection**: The quality of pipes largely depends on the quality of raw materials used. Manufacturers often select steel or other alloys that possess the right characteristics for the intended application. Regular inspections of raw materials help in monitoring their compliance with predefined chemical and physical standards.
2. **Forming**: In this stage, raw materials are shaped into pipe profiles. Various forming methods such as extrusion, spiral welding, and electric resistance welding (ERW) are employed, depending on the pipe type and application. Quality control during this phase includes assessing the machinery alignment and monitoring temperature parameters to ensure consistent material properties.
3. **Welding**: Welding quality is critical, as it's the process that brings together pipe segments. Automated welding systems coupled with real-time monitoring technology can detect defects such as incomplete penetration, undercutting, and porosity. Non-destructive testing (NDT) methods like ultrasonic testing (UT) and radiographic testing (RT) are often integrated to ensure weld integrity.
4. **Sizing**: After welding, pipes undergo size adjustments to meet specific dimensional requirements. This stage utilizes sizing mills that apply controlled pressure to shape the product accurately. Regular calibration of sizing equipment is paramount to maintain precision and compliance with specifications.
5. **Heat Treatment**: Heat treatment processes such as annealing or normalizing can significantly enhance the mechanical properties of the pipes. Quality control measures during this stage include monitoring temperature profiles and soak times, as deviations can lead to inconsistent material properties.
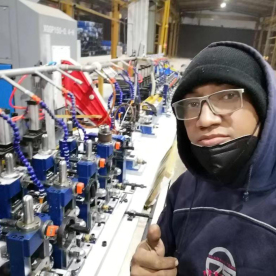
An In-Depth Exploration of Pipe Mill Production Line with Emphasis on Quality Control Measures for Enhanced Operational Efficiency
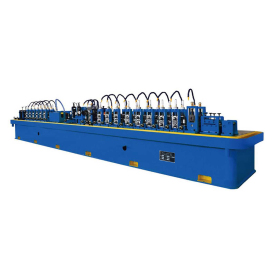
An In-Depth Exploration of Pipe Mill Production Line with Emphasis on Quality Control Measures for Enhanced Operational Efficiency

An In-Depth Exploration of Pipe Mill Production Line with Emphasis on Quality Control Measures for Enhanced Operational Efficiency
Quality control at every stage of the pipe mill production line is essential for ensuring product reliability and compliance with industry standards. Here are some key quality control measures utilized:
1. **In-Process Inspections**: Regular inspections during production help identify potential defects early in the process, reducing waste and the need for rework. Various tests, such as tensile and hardness testing, evaluate the mechanical properties of the materials being processed.
2. **Statistical Process Control (SPC)**: SPC techniques, including control charts and process capability analysis, are employed to monitor production processes in real-time. By analyzing data trends, manufacturers can make informed decisions about process adjustments, maintaining quality and mitigating risks.
3. **Standard Operating Procedures (SOPs)**: The development and adherence to SOPs ensure that every team member follows defined protocols throughout the production process. These documents serve as a reference for best practices in machinery operation, quality checks, and safety measures.
4. **Final Product Testing**: Once manufacturing is complete, products undergo rigorous testing to verify their functionality and safety. This includes pressure testing, leak testing, and dimensional inspections, ensuring that the pipes meet both internal and external quality standards.
5. **Documentation and Feedback Loop**: Maintaining thorough documentation throughout the production and quality control processes provides valuable insights for future improvement. Establishing a feedback loop allows for continuous evaluation of quality measures and operational effectiveness.
**Conclusion**
The integration of quality control measures into the pipe mill production line is not merely a regulatory requirement; it is a fundamental strategy for sustaining operational excellence and product reliability. By investing in robust quality control protocols, manufacturers can ensure that they meet the increasing demands of the market while maintaining high levels of customer satisfaction. As technology progresses, the continued refinement of quality control measures will be pivotal in defining the future landscape of the pipe manufacturing industry.