[High-precision tube making machine ]Revolutionizing Manufacturing Efficiency with High-Precision Tube Making Machines: A Comprehensive Overview of Their Importance and Applications
News 2024-12-3
****In today’s fast-paced industrial landscape, precision and efficiency are paramount. Among the most significant technological advancements that have transformed manufacturing processes is the high-precision tube making machine. These machines play a critical role in numerous industries, including automotive, aerospace, medical, and construction. This article delves deep into the workings, benefits, and applications of high-precision tube making machines, shedding light on why they are indispensable in modern manufacturing.
Understanding High-Precision Tube Making Machines
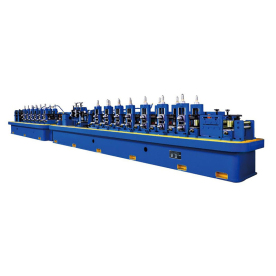
Revolutionizing Manufacturing Efficiency with High-Precision Tube Making Machines: A Comprehensive Overview of Their Importance and Applications
Key Features of High-Precision Tube Making Machines
1. **CNC Control Systems**: Most high-precision tube making machines are equipped with CNC technology, allowing for automated control of the manufacturing process. This results in enhanced precision, reduces human error, and improves production speed.
2. **Versatility**: These machines can produce tubes of various materials—including stainless steel, aluminum, and brass—in different sizes and thicknesses. Their adaptability makes them suitable for multiple sectors.
3. **Quality Assurance**: Many machines come with integrated inspection systems that monitor dimensional accuracy and surface quality in real-time. This ensures that each product meets the required specifications before leaving the production line.
4. **Efficiency**: With the ability to produce large quantities in a short timeframe, high-precision tube making machines significantly enhance operational efficiency, reducing lead times and costs.
Benefits of High-Precision Tube Making Machines
The introduction of high-precision tube making machines in manufacturing has brought numerous benefits:
1. **Improved Accuracy and Consistency**: These machines deliver exceptional accuracy, which is critical for components that interplay with other parts in complex assemblies. The consistent production of high-quality tubes reduces the likelihood of defects, thereby enhancing overall product reliability.
2. **Cost-effectiveness**: While the initial investment in high-precision machines may be substantial, the long-term savings are significant. Reduced material wastage due to precise cutting, lower labor costs from automation, and diminished rework expenses contribute to a favorable return on investment.
3. **Enhanced Production Speed**: High-precision tube making machines can operate continuously, producing large volumes of tubes without compromising quality. This rapid production capability meets the demands of industries requiring just-in-time manufacturing.
4. **Customization Capabilities**: Manufacturers can easily adjust settings to produce custom tube sizes and shapes, catering to specific client needs while maintaining production efficiency.
Applications Across Industries
High-precision tube making machines find applications in various industries, demonstrating their versatility and importance:
1. **Automotive Industry**: High-precision tubes are essential for fuel lines, exhaust systems, and structural components. The automotive sector demands high-quality, durable tubes to ensure safety and performance.
2. **Aerospace Industry**: Aerospace applications require meticulous attention to detail and a high level of reliability. Tubes for hydraulic systems, fuel systems, and airframe structures must withstand high pressures and extreme conditions.
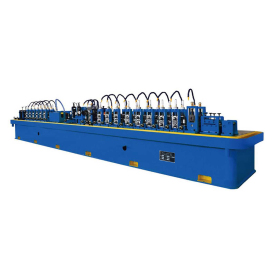
Revolutionizing Manufacturing Efficiency with High-Precision Tube Making Machines: A Comprehensive Overview of Their Importance and Applications
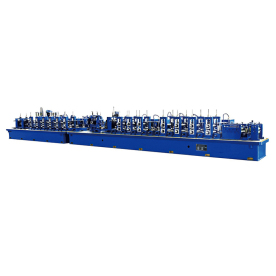
Revolutionizing Manufacturing Efficiency with High-Precision Tube Making Machines: A Comprehensive Overview of Their Importance and Applications
5. **Furniture and Design**: The design industry increasingly utilizes high-precision tubes for modern furniture and architecture, where aesthetics and structural integrity are equally essential.
Conclusion
The evolution of high-precision tube making machines marks a significant advancement in manufacturing technology. By enhancing accuracy, consistency, and efficiency, these machines are transforming how industries approach production. As the demand for precision-engineered products continues to rise, the role of high-precision tube making machines will undoubtedly expand, underscoring their invaluable contribution across a multitude of sectors. Embracing this technology is crucial for manufacturers aiming to thrive in an increasingly competitive market.