[Durable Mould for Tube Mills]Enhancing Productivity and Longevity with Durable Mould for Tube Mills: A Comprehensive Guide for Manufacturers
News 2024-12-2
In the world of manufacturing, particularly in the tube mill industry, ensuring efficiency and durability in the production process is vital. One of the key components that significantly impacts productivity is the mould used in various forming processes. This article explores the importance of selecting durable moulds for tube mills, focusing on their design, material selection, and maintenance practices aimed at maximizing the lifespan and performance of these essential tools.
Understanding the Role of Moulds in Tube Mills
Moulds are integral components in tube mills, guiding raw materials through various stages of processing. They play a critical role in shaping and forming the final product, ensuring that tubes meet the specified dimensions, tolerances, and surface finishes. A durable mould not only enhances the quality of the finished tube but also contributes to overall operational efficiency and productivity.
Characteristics of Durable Moulds
When discussing durable moulds for tube mills, several key characteristics come into play:
1. **Material Composition**: The choice of material used in mould construction is paramount. High-quality steels, often alloyed with elements such as chromium, nickel, or molybdenum, can enhance hardness and wear resistance. Advanced materials like carbide can also be utilized for specific applications where extreme durability is necessary.
2. **Heat Treatment**: Proper heat treatment processes can significantly improve the hardness and performance of moulds. Quenching and tempering techniques can provide the necessary toughness and resilience for challenging manufacturing environments, making them suitable for high-speed production lines.
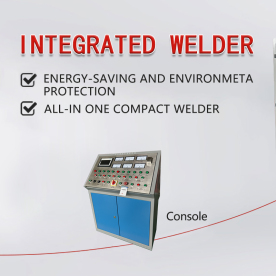
Enhancing Productivity and Longevity with Durable Mould for Tube Mills: A Comprehensive Guide for Manufacturers
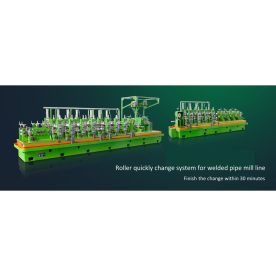
Enhancing Productivity and Longevity with Durable Mould for Tube Mills: A Comprehensive Guide for Manufacturers
The Importance of Maintenance
Even the most durable moulds require regular maintenance to ensure optimal performance in tube mills. Effective maintenance practices can help manufacturers anticipate wear and tear and allow for timely interventions. Here are some vital maintenance tips:

Enhancing Productivity and Longevity with Durable Mould for Tube Mills: A Comprehensive Guide for Manufacturers
2. **Cleaning and Lubrication**: Maintaining clean mould surfaces is crucial. Accumulation of debris can lead to defects in the produced tubes and increase wear on the mould. Additionally, applying the appropriate lubricant can help reduce friction, further extending the mould's life.
3. **Professional Repair Services**: When a mould shows signs of significant wear or damage, seeking professional repair services can be a cost-effective alternative to total replacement. Skilled technicians can assess the mould's condition and make necessary repairs, restoring its functionality.
4. **Training Staff**: Investing in training for production staff about the importance of mould maintenance can foster a culture of care and diligence. Proper training ensures that employees know how to handle moulds correctly, follow maintenance protocols, and recognize when issues may arise.
Conclusion
In conclusion, investing in durable moulds for tube mills is crucial for manufacturers striving for efficiency, superior quality, and longer-lasting products. The right combinations of material composition, heat treatment, and precision design contribute to mould longevity, ultimately impacting the overall productivity of the manufacturing process. By implementing robust maintenance practices and training staff on their importance, manufacturers can enhance the life cycle of their moulds, leading to improved performance and lower operational costs. In an ever-evolving manufacturing landscape, prioritizing durability in mould design and maintenance practices is not just an option; it is a necessity for staying competitive and meeting the high standards of today's markets.