[High frequency welder for metal]Exploring the Benefits and Applications of High Frequency Welders for Metal Fabrication in Modern Industries
News 2024-12-2
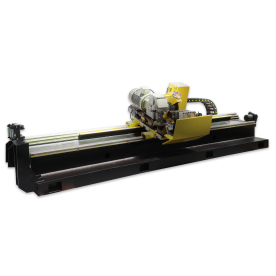
Exploring the Benefits and Applications of High Frequency Welders for Metal Fabrication in Modern Industries
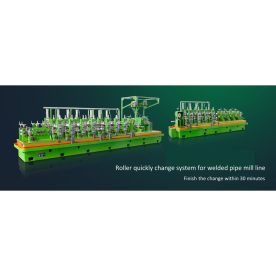
Exploring the Benefits and Applications of High Frequency Welders for Metal Fabrication in Modern Industries
**Understanding High Frequency Welding**

Exploring the Benefits and Applications of High Frequency Welders for Metal Fabrication in Modern Industries
**Benefits of High Frequency Welders for Metal**
1. **Speed and Efficiency**: High frequency welders are known for their rapid welding capabilities. The ability to generate heat instantly means that the welding process can be completed in a fraction of the time compared to traditional methods. This efficiency translates to higher production rates and decreased manufacturing costs.
2. **Precision and Quality**: High frequency welding allows for precise control over the parameters of the welding process, such as temperature and pressure. This level of control leads to higher quality welds with minimal distortion and fewer defects. As a result, manufacturers can achieve consistent quality across large volumes of products.
3. **Versatility**: High frequency welders can be used with various types of metals, including aluminum, copper, and stainless steel. This versatility makes them suitable for a wide range of applications, from automotive and aerospace to construction and electrical industries.
4. **Reduced Material Waste**: The targeted nature of high frequency welding minimizes the amount of heat affected zone (HAZ), reducing the likelihood of warping or damaging surrounding materials. This feature is particularly beneficial in industries where material conservation is critical.
5. **Eco-Friendly**: With a growing emphasis on sustainability, high frequency welding presents an eco-friendly alternative to traditional welding methods that often produce harmful fumes and require excessive energy. The shorter welding times and reduced energy consumption make high frequency welders a greener choice for manufacturers.
**Applications of High Frequency Welding**
High frequency welders are employed in various sectors, each benefiting from the unique properties of this welding technique.
- **Automotive Industry**: In automotive manufacturing, high frequency welding is used to create strong joints in components like exhaust systems, fuel tanks, and structural parts. The fast-paced production lines benefit greatly from the efficiency of high frequency welders.
- **Aerospace Applications**: Aerospace manufacturers require high precision and strength in their components. High frequency welding offers the reliability needed for critical parts of aircraft and spacecraft, ensuring safety and performance.
- **Electrical and Electronics**: High frequency welders play a crucial role in the production of electrical components, such as transformers and inductors. The ability to create solid electrical connections quickly and efficiently is vital for the performance of these devices.
- **Construction and Fabrication**: The construction industry utilizes high frequency welding for joining metal frames, support structures, and various architectural components. This method ensures that the joints can withstand structural stresses and loads.
**Conclusion**
High frequency welders for metal represent a significant advancement in welding technology, offering numerous benefits that cater to modern manufacturing needs. From speed and efficiency to sustainability and versatility, these welders have changed the landscape of metal fabrication across various industries. As industries continue to evolve, the demand for high quality and efficient welding solutions will only grow, solidifying the importance of high frequency welding as a critical component in metal fabrication processes. Embracing this technology can lead manufacturers to improved performance, reduced costs, and enhanced product quality, ultimately driving success in a competitive market.