[High frequency welder for plastic]Exploring the Advantages and Applications of High-Frequency Welders for Plastic in Modern Manufacturing Processes
News 2024-12-2
In today's rapidly evolving manufacturing landscape, the need for efficient and reliable methods of joining materials is more critical than ever. One such method that has gained traction in various industries is the use of high-frequency welders for plastic. This technology offers remarkable benefits, making it an ideal choice for numerous applications, from automotive components to consumer goods. In this article, we will delve into the functioning, advantages, and diverse applications of high-frequency welders for plastic, illuminating why this technology is a key player in modern manufacturing.
Understanding High-Frequency Welding
High-frequency welding, also known as dielectric welding or radio frequency (RF) welding, is a process that employs electromagnetic energy to generate heat within dielectric materials, such as plastic. This technique is particularly effective for thermoplastic materials, which become soft and pliable when heated. The process involves placing the two plastic parts to be joined between two electrodes. When high-frequency electromagnetic waves are applied, the molecules within the plastic vibrate, generating heat and causing the surfaces to melt. As pressure is applied, the molten surfaces coalesce to form a strong bond upon cooling.
One of the defining characteristics of high-frequency welding is its ability to create hermetic seals, which are especially valuable in applications where a secure and airtight union is crucial.
Advantages of High-Frequency Welders for Plastic
1. **Speed and Efficiency**: High-frequency welding is a fast-paced process. The entire cycle, from set-up to completion, can take just a few seconds, making it a highly efficient choice for high-volume production. Manufacturers can benefit significantly from reduced cycle times, resulting in increased output and productivity.
2. **Strong and Reliable Bonds**: The welds produced through this method are incredibly robust, often exceeding the strength of the parent material. This durability ensures that products can withstand various stresses and environmental conditions without compromising integrity.
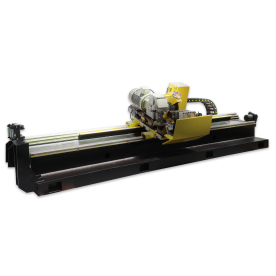
Exploring the Advantages and Applications of High-Frequency Welders for Plastic in Modern Manufacturing Processes
4. **Minimal Surface Preparation**: Unlike other welding techniques, high-frequency welding requires minimal surface treatment. The process can effectively join materials without the need for adhesives or additional bonding agents, simplifying production and reducing costs.
5. **Environmentally Friendly**: Because high-frequency welding does not utilize harmful chemicals or create significant waste products, it is considered an environmentally friendly option. Furthermore, the absence of adhesives and solvents means a reduction in volatile organic compounds (VOCs), making it safer for workers and the environment.
Applications of High-Frequency Welders for Plastic
High-frequency welders for plastic find applications across a multitude of industries:
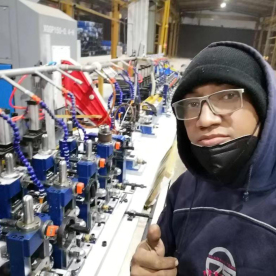
Exploring the Advantages and Applications of High-Frequency Welders for Plastic in Modern Manufacturing Processes
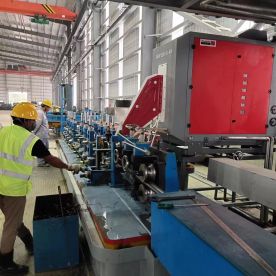
Exploring the Advantages and Applications of High-Frequency Welders for Plastic in Modern Manufacturing Processes
3. **Consumer Products**: High-frequency welding is prevalent in the production of consumer goods, including inflatable toys, outdoor gear, and waterproof clothing. The ability to create strong, leak-proof seals makes it an ideal choice for products exposed to water or other challenging environments.
4. **Packaging Industry**: High-frequency welding is employed to manufacture packaging solutions, such as blisters and pouches. The airtight seals ensure product freshness while extending shelf life.
5. **Aerospace**: In aerospace manufacturing, weight and strength are paramount. High-frequency welders are utilized for bonding lightweight materials in various aviation components, ensuring both safety and performance.
Conclusion
The integration of high-frequency welders for plastic in manufacturing processes marks a significant advancement in efficient and effective material joining techniques. With advantages such as speed, versatility, and environmentally friendly operations, high-frequency welding is set to remain a crucial element in the future of manufacturing across industries. As technology continues to evolve, the applications for high-frequency welders will likely expand, offering innovative solutions to meet the growing demands of manufacturers worldwide.