[Industrial-grade induction heating equipment]Unlocking Efficiency and Innovation: The Role of Industrial-Grade Induction Heating Equipment in Modern Manufacturing Processes
News 2024-12-1
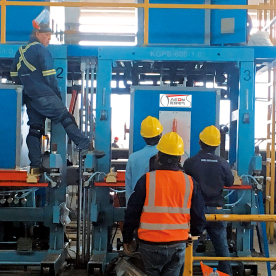
Unlocking Efficiency and Innovation: The Role of Industrial-Grade Induction Heating Equipment in Modern Manufacturing Processes
Understanding Induction Heating
At its core, induction heating is a process that uses electromagnetic induction to heat conductive materials. The technology operates by generating high-frequency electric currents, which create magnetic fields. These fields induce heat in the workpiece, allowing it to reach the desired temperature quickly and uniformly without external heat sources. The primary advantage of induction heating is its efficiency, as it minimizes heat loss and can significantly reduce energy consumption compared to conventional heating methods.
Industrial-grade induction heating equipment is designed to withstand the rigorous demands of industrial applications. It typically features robust construction, capable of enduring high temperatures and continuous operation. From metal fabrication and forging to surface hardening and heat treating, these machines play a critical role across a range of industries, including automotive, aerospace, and manufacturing.
Applications of Industrial-Grade Induction Heating
1. **Metal Hardening and Tempering:** One of the most prominent applications of industrial-grade induction heating equipment is in the hardening and tempering of metals. This process involves rapidly heating components to a specific temperature and then cooling them down to increase their hardness and strength. Induction heating allows for precise temperature control, which is crucial for producing high-quality components that meet stringent specifications.
2. **Brazing and Soldering:** Induction heating is also widely used in brazing and soldering applications, where it enables the joining of dissimilar metals without compromising their structural integrity. The equipment provides localized heating, which minimizes thermal distortion and ensures that the joint is clean and strong. This capability is particularly beneficial in industries like electronics and plumbing, where precision and reliability are paramount.
3. **Melting and Casting:** The melting of metals is another significant application of industrial-grade induction heating systems. These systems offer rapid melting times and energy efficiency, making them ideal for foundries and metalworking shops. Induction furnaces can melt various types of metals, including steel, aluminum, and copper, providing flexibility and versatility for manufacturers.
4. **Heat Treatment Processes:** Industrial-grade induction heating equipment is essential for various heat treatment processes, such as annealing, normalizing, and surface hardening. By controlling the heating rate and temperature profile, manufacturers can achieve desired material properties, such as increased ductility or improved wear resistance. This precision ensures that the final products meet the rigorous demands of modern applications.
5. **Quality Control:** In addition to its role in production, industrial-grade induction heating equipment assists in quality control. The uniform heating patterns achieved through induction processes help eliminate defects caused by uneven heating, such as warping or cracking. This consistency leads to improved product quality and reliability, which is crucial for maintaining competitive advantages in the market.
Benefits of Using Industrial-Grade Induction Heating Equipment
1. **Energy Efficiency:** One of the most compelling arguments for adopting industrial-grade induction heating is its energy efficiency. The targeted heating process can lead to substantial energy savings compared to traditional heating methods, reducing both operational costs and the environmental impact of manufacturing processes.
2. **Enhanced Safety:** Induction heating systems are inherently safer than conventional heating systems. As they do not involve open flames or hot surfaces, the risk of fires and burns is significantly reduced. Additionally, automation in temperature control minimizes the chances of human error during heating processes.
3. **Improved Process Speed:** The rapid heating capabilities of induction equipment allow for shorter processing times. This speed not only enhances productivity but also enables manufacturers to meet tight deadlines and reduce lead times for their products, ultimately improving customer satisfaction.
4. **Reduced Material Waste:** By providing precise heat control and minimizing overheating, industrial-grade induction heating equipment significantly reduces material waste. This efficiency aligns with the growing demand for sustainable practices within the manufacturing sector.
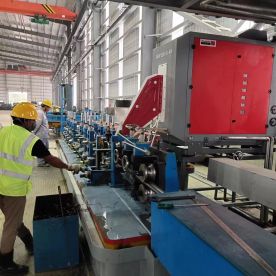
Unlocking Efficiency and Innovation: The Role of Industrial-Grade Induction Heating Equipment in Modern Manufacturing Processes
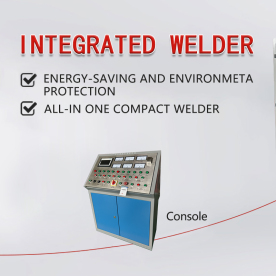