[Cold Cutting Saw Machine for Metal]Revolutionizing Metal Fabrication: The Advantages of Using a Cold Cutting Saw Machine for Metal Processing
News 2024-11-30
****In today’s fast-paced manufacturing environment, precision and efficiency are key drivers for producing high-quality metal products. One of the most significant advancements in metal cutting technology has been the introduction of the cold cutting saw machine. This innovative equipment provides numerous advantages over traditional cutting methods, ensuring that metal fabrication companies can meet the increasing demands of their clients while maintaining high standards of quality and safety.
A cold cutting saw machine operates at lower temperatures than traditional cutting methods. As the name implies, the process does not rely on heat to slice through metal. Instead, it uses a toothed circular saw blade, typically made of high-speed steel or carbide, to cut through the material with a combination of pressure and rotational motion. This method is particularly effective for cutting ferrous and non-ferrous metals, including stainless steel, aluminum, and brass.
One of the standout benefits of using a cold cutting saw machine for metal processing is its ability to produce clean, burr-free edges. When using traditional cutting methods, heat generation can lead to melting, warping, or burning, which compromises the integrity of the cut. Cold cutting minimizes these issues by eliminating heat buildup, resulting in smoother edges that require less finishing work. This not only improves the appearance of the final product but also enhances the overall efficiency of the manufacturing process, as less time needs to be spent on post-cutting operations.
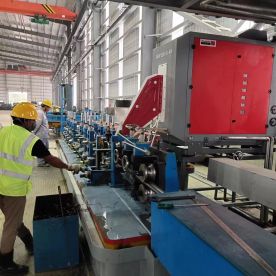
Revolutionizing Metal Fabrication: The Advantages of Using a Cold Cutting Saw Machine for Metal Processing
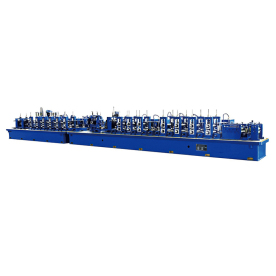
Revolutionizing Metal Fabrication: The Advantages of Using a Cold Cutting Saw Machine for Metal Processing
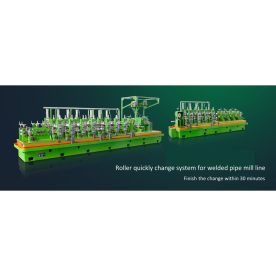
Revolutionizing Metal Fabrication: The Advantages of Using a Cold Cutting Saw Machine for Metal Processing
Moreover, cold cutting saw machines are versatile and can accommodate a wide range of materials and thicknesses. This adaptability makes them a valuable addition to any metal fabrication shop, as they can be used for various projects, from simple cuts to complex shapes. As production needs change, the cold cutting saw machine can easily adjust to these demands, providing manufacturers with the flexibility to evolve alongside market trends.
In conclusion, the cold cutting saw machine for metal processing represents a significant step forward in the industry. With its ability to deliver precision cuts, reduce heat-related issues, enhance safety, and improve overall efficiency, it has become an essential tool for metal fabricators striving to stay competitive. As technology continues to advance, adopting such innovations will only become more critical for businesses aiming to provide high-quality products in a rapidly changing marketplace. Managers and operators investing in cold cutting technology are not only future-proofing their operations but also setting a foundation for sustainable growth in the metal fabrication sector.