[Multi-functional tube making machine]Exploring the Advantages and Innovations of Multi-Functional Tube Making Machines in Modern Manufacturing
News 2024-11-30
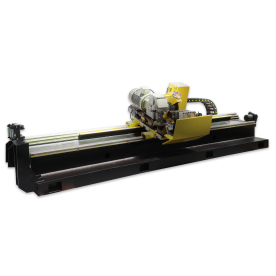
Exploring the Advantages and Innovations of Multi-Functional Tube Making Machines in Modern Manufacturing
In the ever-evolving landscape of manufacturing, efficiency and versatility remain paramount. One key innovation that has garnered significant attention is the multi-functional tube making machine. Designed to streamline production processes while providing a range of functionalities, these machines are transforming how industries produce various types of tubes. Manufacturers increasingly seek equipment that can adapt to multiple production requirements without sacrificing quality or efficiency. In this article, we will delve into the intricacies of multi-functional tube making machines, exploring their design, applications, advantages, and the future they herald in tube manufacturing.
**Understanding Multi-Functional Tube Making Machines**
Multi-functional tube making machines combine various tube manufacturing processes into a single unit, which can include extrusion, cutting, and shaping, among others. This versatility allows manufacturers to produce different types of tubes—plastic, metal, or composite—according to their specific needs. The design of these machines accommodates several factors, such as materials used, tube sizes, and additional aesthetic or functional features.
Typically, a state-of-the-art multi-functional tube making machine integrates advanced technologies such as CNC (Computer Numerical Control), PLC (Programmable Logic Controller), and other automated systems. These technologies facilitate precise control over the production process, ensuring that each tube meets the required specifications and tolerances.
**Key Advantages of Multi-Functional Tube Making Machines**
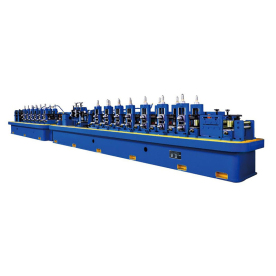
Exploring the Advantages and Innovations of Multi-Functional Tube Making Machines in Modern Manufacturing
2. **Cost-Effectiveness**: By consolidating multiple functions into one machine, companies can reduce the number of machines needed for tube production. This consolidation leads to lower capital investment, reduced operational costs, and savings in maintenance. The efficiency gained from automated systems also translates to faster production cycles, which can significantly help in meeting tight deadlines.
3. **Space Efficiency**: Traditional tube making setups often require several machines stationed in separate areas of a factory, which can take up significant floor space. A multi-functional tube making machine condenses this into a single unit, freeing up vital workspace for other operations or new technologies.
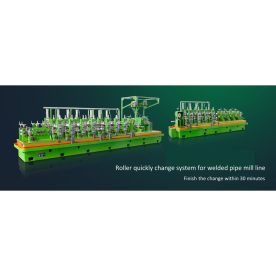
Exploring the Advantages and Innovations of Multi-Functional Tube Making Machines in Modern Manufacturing
5. **Enhanced Automation and Smart Technology**: Multi-functional tube making machines increasingly incorporate smart technology, such as IoT (Internet of Things) connectivity and data analytics. These advancements allow manufacturers to monitor real-time performance, predict maintenance needs, and optimize production processes based on data insights.
**Applications Across Industries**
The applications for multi-functional tube making machines are vast and varied, impacting numerous industries. In the automotive sector, these machines produce tubes for exhaust systems, fuel lines, and hydraulic systems. The medical industry relies on them for sterile tubing used in various applications, from IV lines to catheters. Additionally, industries involved in food and beverage packaging benefit from using these machines to produce hygienic and compliant tubes.
Moreover, electronics and telecommunications industries utilize multi-functional tube making machines for producing protective tubing for wiring and cables, highlighting the machine's adaptability to manufacturing needs across divergent sectors.
**The Future of Tube Manufacturing**
As technology continues to advance, the future of multi-functional tube making machines looks promising. With the persistent push for sustainability, manufacturers are increasingly seeking machines that can not only produce tubes efficiently but also from eco-friendly materials. Innovations in material science may lead to the development of biodegradable tubes and advanced composites that offer higher performance with a lower environmental impact.
Furthermore, the integration of AI (Artificial Intelligence) into tube manufacturing may optimize production further by anticipating patterns in demand, quality control, and predictive maintenance. As manufacturers strive for continual improvement, the role of multi-functional tube making machines will only grow in importance.
In conclusion, multi-functional tube making machines signify a significant leap forward in manufacturing efficiency, versatility, and quality. As industries evolve, these machines will undoubtedly play a crucial role in shaping the future of tube production, making them indispensable tools in a wide range of applications. Closing the gap between cost, quality, and environmental responsibility remains a challenge, but with ongoing innovations and advances, the possibilities are vast and exciting.