[Mould for tube mill]Understanding the Importance of Mould for Tube Mill: Enhancing Efficiency and Quality in Tube Manufacturing Processes
News 2024-11-30
****In the world of manufacturing, especially when it comes to metal processing, the tube mill is a critical machine used for producing various types of tubes and pipes. Central to the operation of a tube mill is the mould, which plays an essential role in determining the overall quality, efficiency, and consistency of the final product. In this article, we will delve into the significance of the mould for tube mills, exploring its functions, types, materials, and the impact it has on manufacturing processes.
What is a Tube Mill?
A tube mill is a type of machinery used to form continuous rolls of metal sheets into tubes or pipes. These machines are extensively utilized in industries such as construction, automotive, and energy, where tubular components are fundamental. The process typically begins with flat metal strips, which are gradually shaped and welded to form a tube. The mould is crucial to this process, as it determines the final dimensions and shape of the tube.
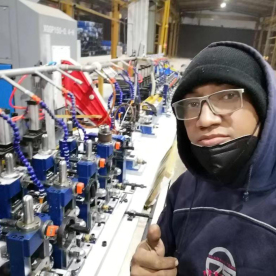
Understanding the Importance of Mould for Tube Mill: Enhancing Efficiency and Quality in Tube Manufacturing Processes
The mould in a tube mill serves several essential functions:
1. **Shape Determination**: The mould defines the internal and external diameters of the pipe, ensuring that the formed tube meets specific dimensional requirements. This is crucial in many applications, where precise measurements are necessary for proper fitting and functionality.
2. **Support during Forming**: During the forming process, the mould provides support to the metal as it transitions from a flat strip to a rolled tube shape. This support helps prevent deformation and ensures the integrity of the tube during the welding process.
3. **Heat Dissipation**: In some instances, the welding process can generate significant heat. The mould can help dissipate heat away from the welded area, thus preventing warping and preserving the metallurgical properties of the metal.
4. **Surface Finish**: The mould's interior can also influence the surface finish of the finished tube. A well-designed mould can minimize surface imperfections, enhancing the aesthetic and functional quality of the product.
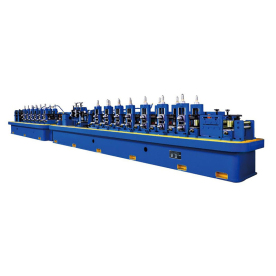
Understanding the Importance of Mould for Tube Mill: Enhancing Efficiency and Quality in Tube Manufacturing Processes
The choice of mould can vary significantly based on the type of tube being produced. Generally, moulds can be categorized into two main types: fixed and adjustable.
1. **Fixed Moulds**: These moulds are static and are used for producing tubes with a fixed diameter. They tend to offer high precision and consistency, making them suitable for mass production of standard-sized tubes.
2. **Adjustable Moulds**: These moulds allow operators to change dimensions easily, making them versatile for producing a range of tube sizes and shapes. While they might not offer the same level of precision as fixed moulds, they provide flexibility for manufacturers to meet various market demands.
Materials Used in Mould Fabrication
The materials selected for mould fabrication are crucial for ensuring durability and performance. Common materials include:
1. **Steel**: High-strength steel is often used owing to its rigidity and ability to withstand high pressure and temperature during the tube formation process.
2. **Aluminum**: Lightweight and resistant to corrosion, aluminum moulds are sometimes preferred for specialized applications, although they may not support as much weight as steel options.
3. **Copper and Bronze**: These materials are less common but may be employed in applications where heat exchange properties are essential.
4. **Composite Materials**: In more advanced applications, composite materials are gaining traction due to their lightweight and high-strength properties, providing an excellent alternative to traditional metals.
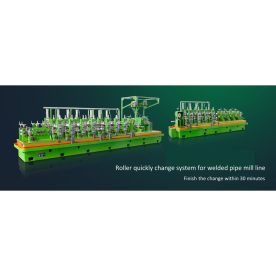
Understanding the Importance of Mould for Tube Mill: Enhancing Efficiency and Quality in Tube Manufacturing Processes
The quality of the mould directly affects the efficiency of the tube mill process and the quality of the final product. A well-designed and manufactured mould can reduce material waste by ensuring that the tubes are formed correctly the first time, thus minimizing the need for rework or scrap. Additionally, by achieving consistent tolerances, manufacturers can enhance their product’s marketability and reliability.
Moreover, modern mould technologies, including computer-aided design (CAD) and computer numerical control (CNC) machining, have significantly advanced the precision of moulds, leading to better manufacturing outcomes. The ability to prototype mould designs digitally allows manufacturers to optimize the moulds before committing to physical production, reducing lead times and costs.
Conclusion
In summary, the mould for tube mills is an integral component that influences the entire tube manufacturing process. From determining the tube's dimensions to providing stability during formation, the mould ensures that manufacturers produce high-quality products efficiently. Understanding the various types of moulds, materials used, and their impacts on the manufacturing process can aid industry professionals in making informed decisions that enhance product quality and operational efficiency. Investing time and resources into optimizing mould design and material selection is essential for any tube manufacturing business aiming to succeed in a competitive market.