[High-precision tube making machine ]Revolutionizing Manufacturing with High-Precision Tube Making Machines: Efficiency, Accuracy, and Versatility in Modern Production Lines
News 2024-11-30
In today's fast-paced manufacturing environment, the demand for precision and efficiency is greater than ever. Industries ranging from aerospace and automotive to medical equipment and construction require components that adhere to stringent specifications. A significant player in addressing these needs is the high-precision tube making machine. These advanced machines have revolutionized the way tubes are produced, improving quality, reducing waste, and increasing throughput.
A high-precision tube making machine is designed to manufacture tubes with exacting dimensions and tolerances. This capability is essential in numerous applications where the integrity of the tube can directly affect the performance of the final product. For instance, in the medical field, the tubes used in devices must be both precise and consistent to ensure patient safety. Similarly, in automotive applications, the tubes must withstand significant stress and strain, necessitating high-quality production techniques.
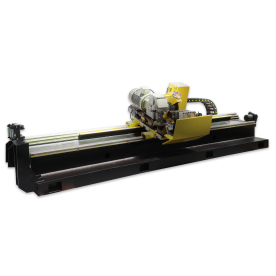
Revolutionizing Manufacturing with High-Precision Tube Making Machines: Efficiency, Accuracy, and Versatility in Modern Production Lines
The advanced technology employed in these machines, including computer numerical control (CNC) systems, enables unprecedented levels of accuracy. CNC technology allows for precise control over the tube forming process, enabling intricate designs and shapes that were previously difficult or impossible to achieve. Coupled with software that can simulate and optimize the manufacturing process, manufacturers can minimize errors and reduce material waste.
Moreover, high-precision tube making machines are often equipped with advanced monitoring and feedback systems. These systems continuously track the production parameters and provide real-time data to operators, allowing for quick adjustments if necessary. This proactive approach not only helps maintain product quality but also leads to reduced downtime, further enhancing overall productivity.
In terms of speed, modern machines can produce tubes at remarkable rates without compromising quality. Automation has played a crucial role in this advancement, with machines designed to perform multiple tasks seamlessly — from cutting and bending to welding and finishing. This eliminates the need for manual intervention, reducing the risk of human error and enabling operators to focus on more critical aspects of production.
Economically, investing in high-precision tube making machines can have a profound impact on a company’s bottom line. By improving accuracy and consistency, businesses can reduce scrap and rework rates, translating to significant cost savings. Moreover, the ability to produce high-quality products consistently can lead to enhanced customer satisfaction, fostering long-term business relationships and repeat orders.
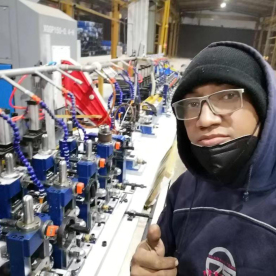
Revolutionizing Manufacturing with High-Precision Tube Making Machines: Efficiency, Accuracy, and Versatility in Modern Production Lines
It is essential to highlight the impact of high-precision tube making machines on sustainability efforts within the manufacturing sector. By optimizing material usage and reducing waste, these machines contribute to more sustainable production practices. Furthermore, their efficiency can help manufacturers lower energy consumption, aligning with the global push towards more environmentally friendly operations.
