[Sharp HSS Blade for Machining Applications]Understanding the Importance of a Sharp HSS Blade for Machining Applications: Enhancing Precision, Efficiency, and Tool Longevity
News 2024-11-29
In the world of machining, the tools used can make a significant difference in the quality and efficiency of completed projects. Among these tools, the High-Speed Steel (HSS) blade stands out due to its versatile applications and impressive performance. However, the effectiveness of an HSS blade largely depends on its sharpness. In this article, we will explore the importance of a sharp HSS blade for machining applications, discussing how it affects precision, efficiency, and the overall lifespan of the tool.
What is HSS?
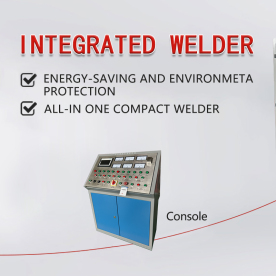
Understanding the Importance of a Sharp HSS Blade for Machining Applications: Enhancing Precision, Efficiency, and Tool Longevity
The Importance of Sharpness in HSS Blades
The sharpness of an HSS blade is critical for several reasons. First and foremost, a sharp blade ensures precision during machining. When the cutting edge is sharp, it can precisely cut through materials without excess force or pressure. This precision minimizes the risk of defects, producing higher quality finishes and reducing the need for additional post-processing work.
Conversely, a dull HSS blade can lead to rough cuts, poor surface finish, and shape inaccuracies that compromise the integrity of the final product. When working with softer materials, a dull blade may cause tearing rather than cutting, resulting in a poorly machined component that fails to meet specifications.
Efficiency and Speed
Another significant advantage of maintaining a sharp HSS blade is the increased efficiency it provides. Machining operations rely heavily on speed, and a sharp blade allows for faster cutting rates. This not only reduces the time taken to complete each part but also improves productivity, as more parts can be processed in a shorter amount of time.
A sharp blade requires less force to achieve the desired cut, which translates into lower energy consumption. This not only has environmental benefits but also reduces wear on the machinery and the blades themselves.
In contrast, using a dull blade leads to increased cutting resistance, resulting in slower operations. This forces operators to exert more force, which can cause strain on machines and lead to faster degradation of both the blades and the equipment.
Longevity and Cost-Effectiveness
Investing in a sharp HSS blade translates into enhanced longevity and cost-effectiveness. Sharp blades have a longer usable life compared to dull ones, which require frequent sharpening or replacement. Regularly sharpening a dull blade can be time-consuming and costly, as it involves downtime that could be spent on production.
In turn, consistently using sharp blades leads to reduced operational costs. The less frequently tools need to be replaced, the lower the overall expenses for the machining operation. Additionally, this practice conserves resources and minimizes waste, aligning with modern sustainability objectives that prioritize efficient use of materials.
Best Practices for Maintaining Sharpness
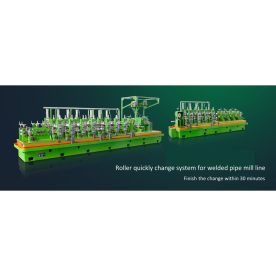
Understanding the Importance of a Sharp HSS Blade for Machining Applications: Enhancing Precision, Efficiency, and Tool Longevity
1. **Regular Inspection**: Regularly check the blades for signs of dullness or damage. Immediate assessment can dictate whether a blade needs sharpening or replacement.
2. **Proper Sharpening Techniques**: Utilize appropriate sharpening tools and techniques suited for HSS blades. Electric grinders specifically designed for HSS can deliver precision sharpening.
3. **Using Correct Parameters**: Understand the material being machined and set the machine parameters accordingly. Avoid excessive feed rates and cutting speeds that can lead to premature dulling.

Understanding the Importance of a Sharp HSS Blade for Machining Applications: Enhancing Precision, Efficiency, and Tool Longevity
Conclusion
In summary, the sharpness of a High-Speed Steel blade is paramount in machining applications. It not only plays a vital role in achieving precision and efficiency, but it also impacts the lifespan of the tool and the overall cost-effectiveness of operations. By prioritizing sharpness through regular maintenance and proper usage, machinists can significantly enhance their productivity and the quality of their finished products. Investing time in keeping HSS blades sharp is an investment in the future success of machining projects, ensuring they meet the highest standards of performance and quality.