[High-precision tube making machine ]Revolutionizing Manufacturing: The Significance of High-Precision Tube Making Machines in Modern Industry
News 2024-11-29
In today’s rapidly evolving manufacturing landscape, precision and efficiency are paramount. Among the technological advancements that have significantly influenced manufacturing processes is the high-precision tube making machine. This sophisticated equipment has revolutionized how tubes are produced, enhancing quality, consistency, and operational efficiency. Its importance spans a wide array of industries, including automotive, aerospace, medical, and construction, where precision tubing is critical to product functionality and safety.
The high-precision tube making machine is engineered to manufacture tubular components that meet rigorous specifications. These machines can produce various types of tubes, including those made from metals, plastics, and composite materials. The precision of these machines is primarily due to advanced computer numerical control (CNC) technology that allows for tight tolerances and complex geometries. This capability is especially crucial in industries demanding strict adherence to quality standards and specifications.
One of the key features of high-precision tube making machines is their ability to execute multiple processes in a single setup, which includes cutting, bending, and forming. Traditional methods of tube production often require several machines to complete these tasks, increasing production time and expenses. In contrast, high-precision machines streamline production by consolidating these processes, thereby enhancing overall productivity and reducing lead times. Manufacturers can respond more rapidly to market demands and customize products to meet specific client requirements, securing a competitive advantage in their respective fields.
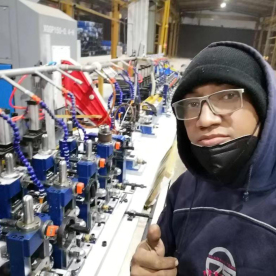
Revolutionizing Manufacturing: The Significance of High-Precision Tube Making Machines in Modern Industry
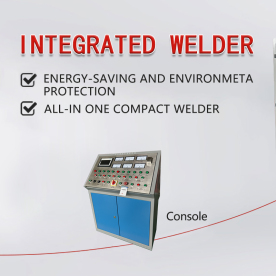
Revolutionizing Manufacturing: The Significance of High-Precision Tube Making Machines in Modern Industry
Energy efficiency is another vital aspect of high-precision tube making machines. In recent years, manufacturers have responded to the growing environmental concerns by developing machines that consume less energy while maximizing output. These energy-efficient models help companies reduce their carbon footprint while also lowering operational costs. More sustainable manufacturing practices are becoming increasingly important, and businesses that prioritize energy efficiency not only contribute to environmental conservation but also stand to benefit from significant cost savings.
The versatility of high-precision tube making machines also cannot be overstated. These machines can accommodate a wide range of materials and can be easily adapted to produce tubes of various sizes and shapes. Whether it’s producing slender tubes for medical applications or robust pipelines for construction, high-precision tube making machines can be tailored to meet diverse manufacturing requirements. This adaptability ensures that manufacturers can pivot their operations to seize new opportunities as market demands arise.

Revolutionizing Manufacturing: The Significance of High-Precision Tube Making Machines in Modern Industry
In conclusion, the high-precision tube making machine represents a groundbreaking advancement in manufacturing technology. Its impact on efficiency, precision, and versatility is reshaping how various industries produce tubing solutions. As the demand for high-quality, precision-engineered components continues to rise, the adoption of high-precision tube making machines will likely expand, further solidifying their role as indispensable tools in modern manufacturing. By investing in these advanced machines, manufacturers can enhance their productivity, streamline operations, and ultimately achieve greater success in an increasingly competitive marketplace.