[Solid state HF welder with wire feed system]Exploring the Advantages and Applications of Solid State HF Welder with Wire Feed System in Modern Manufacturing
News 2024-11-28
In today’s ever-evolving manufacturing landscape, the push for increased efficiency, precision, and cost-effectiveness has led to the development of advanced welding technologies. Among these advancements, the solid state HF (high frequency) welder with a wire feed system stands out as a revolutionary solution for various industrial applications. This article delves into the principles behind this technology, its benefits, and its diverse applications in modern manufacturing.
Understanding Solid State HF Welding
Solid state HF welding is a friction welding method that utilizes high frequency electromagnetic fields to generate heat in the workpieces, enabling them to bond without the need for added materials or significant heat input. The "solid state" aspect of this technology refers to its ability to produce welds through a solid-phase process that mitigates the heat-affected zone (HAZ), thereby preserving the integrity of the base materials.
The incorporation of a wire feed system into solid state HF welding enhances the versatility and efficiency of the welding process. In conventional welding methods, filler materials are often manually fed into the weld pool, which can introduce inconsistencies. However, with an integrated wire feed system, the welding filler is automatically fed, ensuring uniform application and improved weld quality.
Key Advantages of Solid State HF Welder with Wire Feed System
1. **Enhanced Weld Quality**: One of the primary advantages of solid state HF welding is the superior quality of the welds produced. The process minimizes the introduction of impurities and defects, resulting in stronger, more reliable joints. The wire feed system aids in achieving consistent filler material deposition, which contributes further to the integrity of the weld.
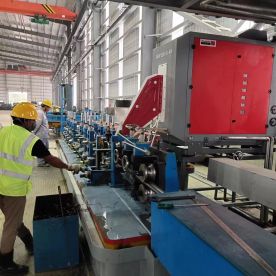
Exploring the Advantages and Applications of Solid State HF Welder with Wire Feed System in Modern Manufacturing
3. **Reduced Heat Input**: Solid state HF welding operates with lower heat inputs compared to traditional welding techniques. This characteristic is particularly beneficial when working with heat-sensitive materials that may warp or become structurally compromised under high temperatures. The controlled heat input ensures that the adjacent areas of the workpieces remain unaffected.
4. **Flexibility in Material Processing**: The versatility of solid state HF welders equipped with wire feed systems allows them to join a variety of materials, including metals, composites, and plastics. This adaptability makes them suitable for a wide range of industries, from automotive manufacturing to aerospace and medical devices.
5. **Lower Operating Costs**: Though the initial investment in solid state HF welding machinery with an integrated wire feed system may be higher than that of traditional systems, the long-term savings are significant. Reduced material waste, lower labor costs, and decreased energy consumption contribute to the overall affordability of the technology.
Applications in Modern Manufacturing
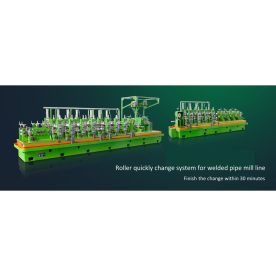
Exploring the Advantages and Applications of Solid State HF Welder with Wire Feed System in Modern Manufacturing
1. **Automotive Industry**: In automotive manufacturing, this technology is used to weld various components, including body panels, frame assemblies, and exhaust systems. The precision and reliability of solid state welding ensure that automotive assemblies meet stringent safety and performance standards.

Exploring the Advantages and Applications of Solid State HF Welder with Wire Feed System in Modern Manufacturing
3. **Medical Devices**: The manufacturing of medical equipment and devices requires stringent quality control and precision. Solid state HF welders with wire feed systems are utilized to ensure that joints used in surgical instruments and devices are both reliable and hygienic.
4. **Electronic Components**: The electronics industry uses solid state welding technology for the assembly of circuit boards and other components. The low heat input ensures that delicate components are not damaged during the welding process.
5. **Construction and Infrastructure**: In the construction sector, solid state HF welding is used for joining structural steel elements, pipelines, and other critical infrastructure components, providing strength and durability to engineered structures.
Conclusion
The solid state HF welder with wire feed system represents a significant leap forward in welding technology. With its enhanced weld quality, efficiency, reduced heat input, flexibility, and cost-effectiveness, it is poised to be an invaluable tool in modern manufacturing. As industries strive for higher standards and more sustainable practices, the adoption of this innovative welding solution will undoubtedly play a crucial role in shaping the future of production processes.