[Customized ERW tube mill solutions]Innovative Approaches to Customized ERW Tube Mill Solutions for Enhanced Manufacturing Efficiency and Product Quality
News 2024-11-27
In the ever-evolving landscape of manufacturing, the demand for specialized equipment that caters to specific needs has never been greater. Among the various machinery that plays a crucial role in steel production, Electric Resistance Welded (ERW) tube mills stand out. These mills are essential for producing high-quality tubular products used across multiple industries, including construction, automotive, and energy. Customized ERW tube mill solutions offer manufacturers the flexibility and precision necessary to meet specific requirements, ultimately leading to improved efficiency and product quality.
Customized ERW tube mill solutions involve the tailoring of machinery to fit unique production needs, which can include variations in tube size, thickness, and material properties. This customization is key for businesses aiming to stay competitive in a global market that increasingly demands versatility and innovation. By investing in a bespoke ERW tube milling system, manufacturers can significantly enhance their operational capabilities.
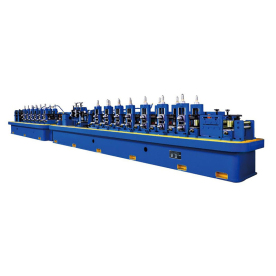
Innovative Approaches to Customized ERW Tube Mill Solutions for Enhanced Manufacturing Efficiency and Product Quality
In addition to material adaptability, customized ERW tube mill solutions can feature advanced technology integrations. Automated systems, for instance, can significantly increase both production speed and consistency. With components like real-time monitoring and feedback loops, these systems can detect discrepancies and make adjustments on the fly, ensuring that every product meets the desired specifications. The integration of Industry 4.0 technologies, such as IoT devices and AI algorithms, can further streamline operations, resulting in reduced downtime and optimized resource utilization.
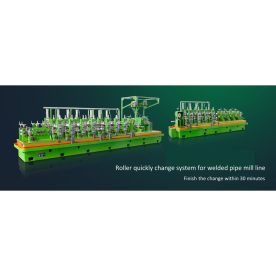
Innovative Approaches to Customized ERW Tube Mill Solutions for Enhanced Manufacturing Efficiency and Product Quality

Innovative Approaches to Customized ERW Tube Mill Solutions for Enhanced Manufacturing Efficiency and Product Quality
Moreover, customized ERW tube mills can enhance environmental sustainability in the manufacturing process. With rising awareness about carbon footprints and waste reduction, many manufacturers are exploring ways to make their operations greener. Innovations such as energy-efficient drives, waste heat recovery systems, and optimized coolant systems can be integrated into customized solutions, effectively lowering the environmental impact of tube production. This commitment to sustainability not only helps preserve the environment but also meets increasingly stringent regulatory standards.
While the initial investment in a customized ERW tube mill solution may seem significant, the long-term benefits often outweigh the costs. The ability to produce a wider variety of products, increase production efficiency, and lower operational costs can lead to higher profitability over time. Additionally, such a strong competitive edge in product offerings can result in higher market share and brand loyalty.
Collaboration with experienced manufacturers and engineers is crucial when developing customized ERW tube mill solutions. Engaging with professionals who understand the nuances of tube production, as well as the specific needs of different industries, ensures that the final solution is both practical and innovative. During the design and implementation phases, feedback from operators and production teams can provide invaluable insights that lead to better equipment performance and increased worker safety.
In conclusion, customized ERW tube mill solutions are indispensable for manufacturers looking to thrive in today’s complex market. By prioritizing personalization, integrating advanced technologies, and maintaining a commitment to sustainability, companies can enhance their production capabilities and improve product quality. In an industry where precision and adaptability are paramount, the right investment in customized ERW tube mill solutions can provide a solid foundation for future growth and success. Embracing these innovative approaches not only elevates manufacturing efficiency but also sets the stage for long-term competitiveness.