[Advanced induction heating equipment technology]Exploring Advanced Induction Heating Equipment Technology: Revolutionizing Industries with Cutting-Edge Heating Solutions
News 2024-11-27
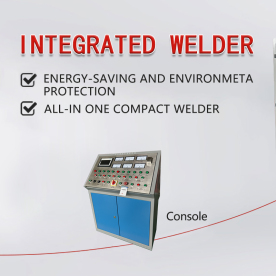
Exploring Advanced Induction Heating Equipment Technology: Revolutionizing Industries with Cutting-Edge Heating Solutions
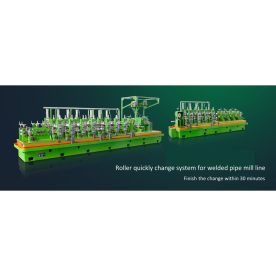
Exploring Advanced Induction Heating Equipment Technology: Revolutionizing Industries with Cutting-Edge Heating Solutions
Induction heating works on the principle of electromagnetic induction, where a high-frequency alternating current passes through a coil, generating a magnetic field. When an electrically conductive material, such as metal, is placed within this field, eddy currents are induced, resulting in rapid heating of the material. The process provides several advantages over traditional heating methods, including instantaneous heating, localized temperature control, and improved energy efficiency.
One of the most notable advancements in induction heating equipment technology is the development of high-frequency induction heaters. These systems are designed to operate at frequencies typically ranging from 1 kHz to several MHz, allowing for faster and more precise heating of small components. Applications such as brazing, soldering, and surface hardening have benefited greatly from these high-frequency systems, enabling manufacturers to achieve tighter tolerances and improved mechanical properties in their products.
Moreover, modern induction heating equipment is equipped with advanced control systems that integrate smart technology for real-time monitoring and feedback. These systems utilize sensors and algorithms to optimize heating processes, ensuring that the correct temperature is reached promptly while minimizing energy consumption. Such integration of smart technology not only enhances efficiency but also enables predictive maintenance, thus reducing downtime and extending the life of the equipment.
Another significant improvement in induction heating technology is the introduction of compact and lightweight designs. Previous induction heating systems were often bulky and required substantial space, making them difficult to integrate into existing production lines. However, the latest models are designed for portability, allowing for easier installation and flexibility in applications. These compact units can be mounted on production fixtures or moved between workstations, which is particularly valuable in small or dynamic manufacturing environments.
Furthermore, advancements in the materials used for induction heating coils have significantly improved the durability and performance of these systems. New high-temperature resistant materials are now employed, allowing for higher operating temperatures and longer lifespans. Additionally, innovations in coil design have optimized the efficiency of heat transfer, ensuring that more energy is utilized effectively in the heating process.
As industries push towards more sustainable practices, the energy efficiency of advanced induction heating equipment technology plays a crucial role. Compared to traditional heating methods, induction heating can reduce energy consumption by up to 70%. This is particularly relevant for processes involving large metal components, where the speed and efficiency of induction heating can lead to lower operational costs. Additionally, the localized heating capabilities of induction systems significantly reduce the heat-affected zone, further minimizing energy waste.
The automotive industry, one of the largest consumers of induction heating technology, is experiencing a transformative phase fueled by these advancements. From hardening steel components to welding aluminum parts, induction heating is becoming an integral part of automotive manufacturing. Manufacturers are increasingly adopting induction heating in the production of electric vehicle components, where precise heating and cooling processes are essential for battery efficiency and performance.
Moreover, the pharmaceutical and food processing industries are also reaping the benefits of advanced induction heating technology. Processes such as sterilization and cooking can be performed with greater control and efficiency, leading to improved product safety and quality. Induction heating ensures that products are heated evenly, eliminating cold spots that could compromise food safety standards.
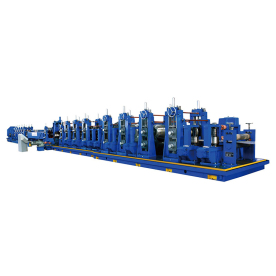