[Precision induction heating equipment]The Future of Metal Processing: How Precision Induction Heating Equipment is Revolutionizing Manufacturing Industries
News 2024-11-23
In today’s fast-paced manufacturing environment, efficiency and precision are paramount. As industries continually seek to optimize their processes, precision induction heating equipment has emerged as a game-changer in metal processing techniques. From automotive to aerospace, this advanced technology offers significant advantages in terms of speed, energy conservation, and material integrity. In this article, we delve into the workings of precision induction heating equipment, its applications, and the myriad benefits it brings to the manufacturing landscape.
What is Precision Induction Heating?
Induction heating is a process that uses electromagnetic induction to generate heat within conductive materials. Precision induction heating equipment operates on the principle of creating an electromagnetic field that induces current in a metal part, resulting in localized heating. Unlike traditional heating methods that often rely on flames or conventional ovens, induction heating is precise and highly controlled. This technology allows manufacturers to heat specific areas of a workpiece rapidly without affecting the surrounding material, making it ideal for a range of applications.
The Mechanism Behind Precision Induction Heating Equipment
At the core of precision induction heating equipment is the induction coil, where alternating current passes through the coil generating an oscillating magnetic field. When a conductive metal such as steel or aluminum is placed within this field, eddy currents are induced, thereby generating heat due to the material’s resistance. This process can achieve high temperatures very quickly, resulting in minimal wait times and superior thermal efficiency.
Moreover, manufacturers can easily adjust the frequency and power settings of the induction heating equipment to target specific heating profiles. This level of control is vital for processes such as hardening, melting, soldering, brazing, and annealing metals, indicating the versatility of this technology.
Applications of Precision Induction Heating Equipment
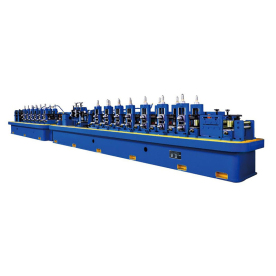
The Future of Metal Processing: How Precision Induction Heating Equipment is Revolutionizing Manufacturing Industries
1. **Automotive Industry**: Induction heating is extensively used for tasks such as hardening gears, bearings, and crankshafts. The precision it offers minimizes distortion and reduces the risk of damaging the components during the heating process.
2. **Aerospace Sector**: The stringent quality standards in aerospace manufacturing demand high precision. Induction heating helps in the assembly of complex parts, ensuring that joints are precisely fused without overheating surrounding materials.
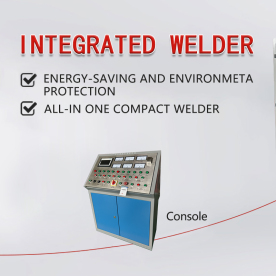
The Future of Metal Processing: How Precision Induction Heating Equipment is Revolutionizing Manufacturing Industries
4. **Tool Making**: Precision induction heating allows for the effective hardening of tools, improving their wear resistance. The ability to focus heat in specific areas makes it possible to enhance specific tool properties while preserving the overall integrity of the tool.
5. **Medical Device Manufacturing**: In an industry that requires utmost precision, induction heating is used in processes like welding implants, ensuring strong and reliable seams.
Advantages of Using Precision Induction Heating Equipment
The benefits of integrating precision induction heating equipment into manufacturing processes are numerous:
- **Efficiency**: Induction heating is incredibly fast compared to traditional methods, which can lead to significant reductions in cycle times.
- **Energy Savings**: As the equipment focuses energy on heating only the required metal part, it greatly reduces wasted energy, making it a more sustainable option.
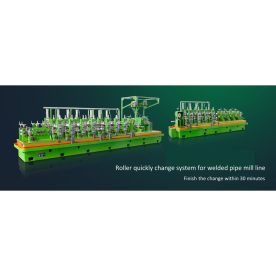
The Future of Metal Processing: How Precision Induction Heating Equipment is Revolutionizing Manufacturing Industries
- **Enhanced Control**: Precision induction heating allows operators to have greater control over the heating process, leading to repeatable results and adherence to stringent quality checks.
- **Safety**: Since the heating element does not produce an open flame, induction heating reduces the risk of fire and other hazards associated with conventional heating methods.
Conclusion
The adoption of precision induction heating equipment marks a significant advancement in the way industries approach metal processing. As the demand for high-quality, efficient, and cost-effective manufacturing solutions continues to rise, this technology is likely to play an increased role across various sectors. By providing substantial benefits in precision, efficiency, and safety, precision induction heating equipment not only streamlines manufacturing processes but also contributes to the overall sustainability goals of modern industries. As innovations in this field continue, the potential for precision induction heating holds great promise for the future of metalworking and manufacturing at large.