[High-Wear-Resistant Spare Parts for Tube Mills]Enhancing Operational Efficiency with High-Wear-Resistant Spare Parts for Tube Mills: A Comprehensive Guide for Manufacturers
News 2024-11-20
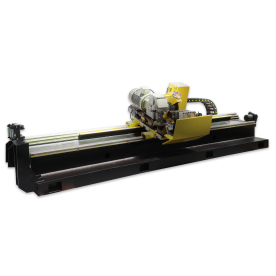
Enhancing Operational Efficiency with High-Wear-Resistant Spare Parts for Tube Mills: A Comprehensive Guide for Manufacturers
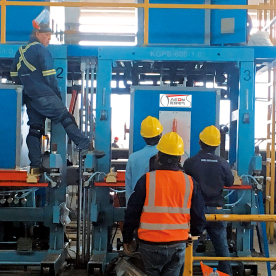
Enhancing Operational Efficiency with High-Wear-Resistant Spare Parts for Tube Mills: A Comprehensive Guide for Manufacturers
Understanding Tube Mills
Tube mills are specialized machines used for the production of metal tubing. These mills use processes like welding, cold forming, and others to shape metal strips into tubes of various dimensions and specifications. Given the repetitive and high-intensity nature of their operations, tube mills are susceptible to wear, often resulting in costly downtimes and maintenance.
The Importance of High-Wear-Resistant Spare Parts
High-wear-resistant spare parts are engineered to endure the rigorous demands of tube milling processes. Traditional spare parts made from standard materials often fail prematurely, leading to frequent replacements and interruptions in production. In contrast, high-wear-resistant alternatives are crafted from advanced materials, such as high chromium steel or other specialized alloys, which exhibit exceptional hardness, toughness, and corrosion resistance.
Benefits of High-Wear-Resistant Spare Parts
1. **Increased Lifespan**: High-wear-resistant components can withstand harsh operating conditions much longer than standard parts. This longevity translates to fewer replacements, saving both time and money.
2. **Reduced Downtime**: By minimizing the frequency of part failure, manufacturers can significantly reduce downtime. This is crucial in high-production environments where every minute counts.
3. **Enhanced Performance**: High-wear-resistant spare parts maintain operational efficiency, as they ensure smooth functioning and consistent product quality. This leads to less rework and scrap, ultimately impacting the bottom line positively.
4. **Cost-Effectiveness**: Although initially more expensive than traditional parts, the long-term savings from reduced maintenance and replacement costs can more than compensate for the upfront investment.
5. **Improved Safety**: Wear and tear can lead to malfunctions, posing safety risks to operators. Using high-wear-resistant components helps ensure machinery operates within safe parameters.
Selecting the Right Spare Parts
When choosing high-wear-resistant spare parts for tube mills, several factors must be considered:
1. **Material Composition**: Research the material properties like hardness, toughness, and resistance to wear and corrosion. Make sure the parts align with the specific needs of the tube milling process.
2. **Supplier Reputation**: Partnering with a reputable supplier that specializes in high-wear-resistant components is vital. Seek those with proven expertise and a track record of delivering reliable products.
3. **Compatibility**: Ensure that the new spare parts are compatible with the existing machinery. This includes checking dimensions, fitting mechanisms, and design specifications.
4. **Technical Support**: A good supplier will also offer technical support, providing insights and advice on the optimal use of their products in your specific tube mill operations.
Best Practices for Maintenance and Installation
To maximize the benefits of high-wear-resistant spare parts, manufacturers should adopt best practices for maintenance and installation:
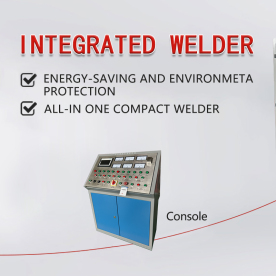
Enhancing Operational Efficiency with High-Wear-Resistant Spare Parts for Tube Mills: A Comprehensive Guide for Manufacturers
2. **Effective Training**: Equip your maintenance team with the necessary training to understand the specifications and installation procedures of high-wear-resistant components fully.
3. **Proper Lubrication**: Ensure that all parts are well-lubricated according to manufacturer specifications. This helps in reducing friction, further prolonging the lifespan of the components.
4. **Documentation**: Keep accurate records of replacement schedules, inspections, and performance metrics to identify trends and areas for improvement in maintenance practices.
Conclusion
The incorporation of high-wear-resistant spare parts into tube mills is not just a preventive measure but a strategic approach to optimizing manufacturing efficiency. By investing in these advanced components, manufacturers can significantly reduce downtime, enhance safety, and improve product quality, ultimately leading to a more sustainable and profitable operation. In an ever-competitive landscape, high-wear-resistant spare parts offer a clear path to achieving a competitive edge and ensuring long-term success.