[Solid state HF welder with remote control]Maximizing Efficiency and Precision in Modern Manufacturing: The Role of Solid State HF Welder with Remote Control Technology
News 2024-11-20
****In the ever-evolving landscape of manufacturing and fabrication, the demand for precision, efficiency, and flexibility continues to grow. One remarkable innovation that addresses these needs is the solid state high-frequency (HF) welder with remote control capabilities. This advanced welding technology offers improved performance, reduces downtime, and enhances the overall quality of welded products. In this article, we will explore the benefits of solid state HF welders equipped with remote control, their applications, and how they represent a significant step forward in the welding industry.
Understanding Solid State HF Welding Technology
Solid state HF welding is a process that utilizes high-frequency electromagnetic energy to join materials, typically metals or thermoplastics, by heating them to their melting point and fusing them together. Unlike traditional welding methods, which often rely on vacuum tubes or microwave generators, solid state welders apply solid-state technology to generate the required frequencies for welding. This advancement results in greater energy efficiency, reduced maintenance, and improved control over the welding process.
The integration of remote control technology into solid state HF welders takes this innovation a step further. Remote control allows operators to manage the welding process from a distance, providing a level of convenience and flexibility that is essential in modern manufacturing environments. This technology is particularly useful when handling large components or in situations where manual operation would be cumbersome or dangerous.
Key Benefits of Solid State HF Welders with Remote Control
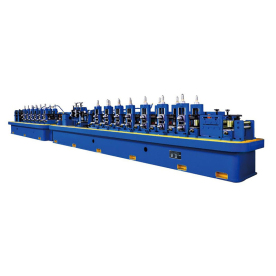
Maximizing Efficiency and Precision in Modern Manufacturing: The Role of Solid State HF Welder with Remote Control Technology
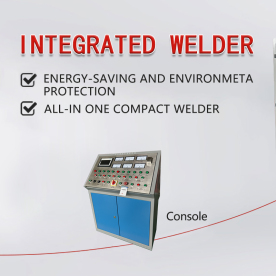
Maximizing Efficiency and Precision in Modern Manufacturing: The Role of Solid State HF Welder with Remote Control Technology
2. **Enhanced Efficiency**: With remote control capabilities, operators can quickly adjust settings without needing to be physically present at the welding machine. This capability drastically reduces downtime, allowing for more efficient operation and higher production rates. Additionally, solid state technology inherently reduces energy consumption, contributing to lower operational costs.
3. **Safety Considerations**: The ability to operate a welder remotely enhances safety in the workplace. Operators can maintain a safe distance from the welding process, minimizing their exposure to potentially harmful conditions such as high temperatures or fumes. This is particularly valuable in industries that deal with hazardous materials or require strict safety protocols.
4. **Flexibility in Operations**: The remote control feature enables real-time adjustments during the welding process. Operators can respond instantly to changing conditions, ensuring that they can maintain optimum performance regardless of the challenges that may arise. This adaptability is crucial in dynamic manufacturing environments where production schedules can shift rapidly.
5. **Reduced Labor Costs**: By streamlining the welding process and allowing operators to manage multiple welding stations from a single location, companies can potentially reduce labor costs. This capability leads to improved workforce allocation and a more streamlined production process.
Applications of Solid State HF Welders
Solid state HF welders with remote control technology find applications across a wide range of industries. In the automotive sector, they are used for welding components in hybrid and electric vehicles, where lightweight materials are increasingly utilized. Additionally, in the electronics industry, solid state HF welding is utilized for joining components in consumer electronics, ensuring high quality and reliability.

Maximizing Efficiency and Precision in Modern Manufacturing: The Role of Solid State HF Welder with Remote Control Technology
Conclusion
The intersection of solid state HF welding technology and remote control capabilities represents a significant leap forward in manufacturing processes. Through improved precision, enhanced efficiency, and increased safety, these advanced welders are revolutionizing the way industries approach welding tasks. As manufacturing continues to evolve, investing in these innovative solutions will not only improve operational efficiency but also lead to higher-quality products and safer work environments. Embracing solid state HF welders with remote control technology is not just a trend but a strategic advantage in today’s competitive market.