[IF pipe seam annealing machine ]Understanding the Role of IF Pipe Seam Annealing Machines in the Modern Pipe Manufacturing Industry
News 2024-11-20
In the modern pipe manufacturing industry, precision and quality are paramount. One of the key components of this process is the IF (Induction Heating) pipe seam annealing machine. This innovative technology has transformed how pipes are produced, ensuring that they meet stringent quality standards while enhancing their mechanical properties. In this article, we will delve into the significance of IF pipe seam annealing machines, exploring their operational principles, benefits, and applications in various industries.
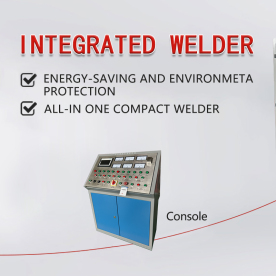
Understanding the Role of IF Pipe Seam Annealing Machines in the Modern Pipe Manufacturing Industry
At their core, IF pipe seam annealing machines are designed to heat the welded seams of pipes to improve their characteristics. The induction heating process utilizes electromagnetic fields to generate heat directly in the material. This method is particularly effective for steel and other ferrous and non-ferrous materials.
During the manufacturing process, pipes are typically formed by welding two edges together. This welded seam can often experience stress and structural weaknesses, which may compromise the pipe's overall integrity. The induction heating process effectively alleviates these issues by softening the metal at the seam, thus allowing for a more uniform microstructure. This results in improved toughness, ductility, and overall performance.
Operational Principles of IF Pipe Seam Annealing Machines
The operation of an IF pipe seam annealing machine begins with the feeding of pipes through the induction heating coil. As the pipe moves through this coil, high-frequency currents generate heat in the metal. The process is highly controllable, allowing manufacturers to adjust parameters such as temperature and exposure time according to specific requirements.
One of the primary advantages of induction heating is its efficiency. Unlike conventional heating methods that heat the entire component, induction heating targets only the areas that require treatment—namely, the welded seams. This localized approach minimizes energy consumption and reduces the risk of overheating or damaging the pipe material.
Benefits of Using IF Pipe Seam Annealing Machines
1. **Enhanced Quality**: The key advantage of IF pipe seam annealing machines is the significant improvement in product quality. By reducing residual stresses and improving the microstructure at the weld, pipes demonstrate better tolerance to pressure and temperature variations.
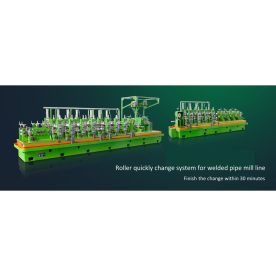
Understanding the Role of IF Pipe Seam Annealing Machines in the Modern Pipe Manufacturing Industry
3. **Lower Energy Costs**: Induction heating is known for its energy efficiency. By heating only specific zones, manufacturers can reduce their energy consumption, resulting in lower operational costs.
4. **Reduced Environmental Impact**: With the push for more sustainable manufacturing practices, the use of induction heating is appealing. The reduced energy consumption and the elimination of harmful emissions associated with traditional heating methods contribute to a lower environmental footprint.
5. **Versatility**: IF pipe seam annealing machines can be adapted to various pipe diameters, wall thicknesses, and materials. This flexibility makes them suitable for a wide range of applications, from oil and gas pipelines to hydraulic systems and beyond.

Understanding the Role of IF Pipe Seam Annealing Machines in the Modern Pipe Manufacturing Industry
IF pipe seam annealing machines find applications in a variety of sectors. In the oil and gas industry, for instance, the enhanced toughness and ductility of pipes are crucial for withstanding high-pressure conditions. Similarly, in construction, reliable pipes are essential for structural integrity and safety.
Moreover, the chemical and pharmaceutical industries benefit significantly from annealed pipes. The improved resistance to corrosion and wear ensures that the pipes maintain their integrity even under challenging conditions, such as exposure to aggressive chemicals.
In conclusion, the IF pipe seam annealing machine is a pivotal asset in the pipe manufacturing industry. Its ability to enhance product quality while reducing production costs makes it invaluable for manufacturers looking to remain competitive. As technology continues to advance, we can expect even greater innovations within this realm, further solidifying the role of induction heating processes in the creation of reliable, high-quality pipes for various applications.