[Roller for tube mill]Enhancing Tube Manufacturing Efficiency: The Crucial Role of Roller Systems in Tube Mills
News 2024-11-18
In the world of metalworking and fabrication, tube mills play a vital role in producing a wide array of tubes used across various industries. From construction to automotive, the demand for quality tube products has surged over the years. As a result, efficient manufacturing processes have become more essential than ever. One of the key components that enhance the performance and efficiency of tube mills is the roller system. This article delves into the importance, types, and advancements in roller technology within tube mills, demonstrating its significance in today’s manufacturing landscape.
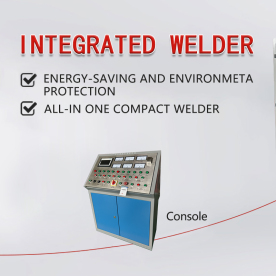
Enhancing Tube Manufacturing Efficiency: The Crucial Role of Roller Systems in Tube Mills
Tube mills are specialized machines designed for creating tubular products from flat metal sheets. These mills use a series of rollers to shape the metal sheets into precise dimensions and tolerances required for various applications. The process involves several stages, including uncoiling, forming, welding, and sizing. While each stage is crucial, the roller system stands out as a pivotal element in determining the overall effectiveness and quality of the end product.
The Role of Rollers in Tube Mills
The primary function of rollers in tube mills is to deform the flat metal strips into a tubular shape. This shaping process is not merely mechanical; it involves several critical factors, including angle of entry, roller position, and forming sequence. Each of these factors impacts the final product's quality, from wall thickness to surface finish.
Moreover, roller systems influence the speed and efficiency of the manufacturing process. High-quality rollers allow for smoother transitions during the shaping process, reducing friction and wear on both the rollers and the material. This decreases the likelihood of defects, such as rippling or uneven seams, which can compromise the structural integrity of the finished tubes.
Types of Rollers Used in Tube Mills
There are several types of rollers used in tube mills, each designed for specific applications and materials.
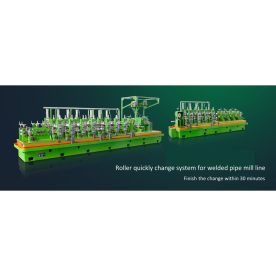
Enhancing Tube Manufacturing Efficiency: The Crucial Role of Roller Systems in Tube Mills
2. **Forming Rollers**: These rollers work to gradually shape the metal into a tube. They are strategically aligned in a sequence that allows the material to take on the desired curvature and dimension without excessive stress.

Enhancing Tube Manufacturing Efficiency: The Crucial Role of Roller Systems in Tube Mills
4. **Sizing Rollers**: After welding, sizing rollers are used to fine-tune the dimensions of the tube. They help achieve the final specified product profile, including diameter and wall thickness.
Innovations in Roller Technology
Advancements in roller technology have significantly impacted the efficiency and quality of tube mills. Innovations such as enhanced materials, computer-aided design (CAD) simulation, and automated roller adjustments have transformed traditional tube manufacturing processes.
- **Material Advancements**: Modern roller systems are often constructed from high-strength alloys that can withstand the intense pressures and temperatures involved in the shaping process. These materials improve durability and reduce the maintenance frequency, which can lead to cost savings.
- **CAD Simulation**: The ability to simulate the forming process using CAD technology allows engineers to optimize roller designs before physical implementation. This results in a more efficient setup with fewer trial-and-error adjustments in the mill.
- **Automation**: Automated systems for adjusting roller positions and settings can improve production speeds and reduce human error. These enhancements contribute to more consistent product quality and a more streamlined manufacturing workflow.
Conclusion
The roller system in tube mills is integral to the manufacturing process of tubular products. By effectively shaping, welding, and sizing metal strips, rollers contribute to the efficiency and quality of the final products. With ongoing technological advancements, the role of rollers in tube mills will only become more significant, enabling manufacturers to meet the rising demand for high-quality tubing in a wide range of applications. As industries evolve, so too must the methods and technologies used in their production, making the continuous improvement of roller systems a crucial aim for tube mill operators worldwide.