[Portable high frequency welder]Exploring the Advantages and Applications of Portable High Frequency Welders for Efficient and Versatile Welding Solutions
News 2024-11-8
In today’s rapidly advancing manufacturing and construction industries, the demand for efficient and convenient welding solutions has never been greater. One of the most innovative tools that have emerged in this landscape is the portable high frequency welder. This versatile device combines advanced technology with mobility, making it an excellent choice for a wide array of welding applications. In this article, we will explore the advantages of portable high frequency welders, their various applications, and why they are becoming indispensable in modern fabrication shops and field projects.
Understanding Portable High Frequency Welders
Before diving into their benefits and uses, it is important to understand what portable high frequency welders are. These machines use high-frequency electrical currents to weld materials, typically thermoplastics and metals. The high-frequency technology allows for precise control over the welding process, resulting in strong, high-quality joints with minimal distortion.
One of the key features of portable high frequency welders is their lightweight design and inherent mobility. This allows users to transport the welder easily from one job site to another, making them ideal for construction sites, workshops, and repair services. Their compact design does not compromise their power or capability, as these welders can handle demanding tasks just as effectively as their stationary counterparts.
Advantages of Portable High Frequency Welders
1. **Mobility and Convenience**: One of the most significant benefits of portable high frequency welders is their mobility. Many welding projects require on-site work, and having a welder that can be easily transported saves time and increases efficiency. Whether in tight spaces, remote locations, or even indoors, a portable welder can reach every corner without the need for extensive setup.
2. **Precision and Control**: High-frequency welding technology offers greater precision compared to traditional welding methods. Users can adjust the frequency and power output to suit different materials and thicknesses. This increased control reduces the chances of defects and ensures a consistent quality of the welded joints.
3. **Versatile Applications**: Portable high frequency welders are suitable for a variety of materials, including metals, plastics, and composites. This versatility makes them ideal for numerous applications such as automotive repairs, fabricating metal structures, or manufacturing plastic products. Whether you are welding PVC pipes or joining aluminum sheets, these welders deliver excellent results.
4. **Efficiency and Speed**: The high-frequency welding process allows for faster welding times compared to conventional methods. This speed not only increases productivity but also significantly reduces labor costs, making projects more cost-effective. The ability to quickly create strong, reliable joints means that workers can move on to the next phase of a project sooner.
5. **Minimal Heat-Affected Zone**: Because high-frequency welding concentrates heat in a small area, the heat-affected zone (HAZ) is minimized. This results in less thermal distortion and damage to the surrounding materials, a crucial advantage in applications where precision and material integrity are paramount.
Applications of Portable High Frequency Welders
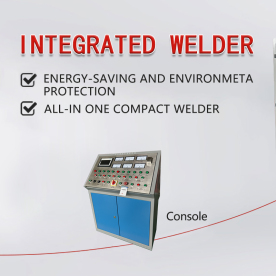
Exploring the Advantages and Applications of Portable High Frequency Welders for Efficient and Versatile Welding Solutions
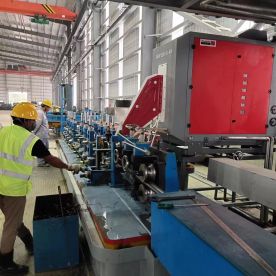
Exploring the Advantages and Applications of Portable High Frequency Welders for Efficient and Versatile Welding Solutions
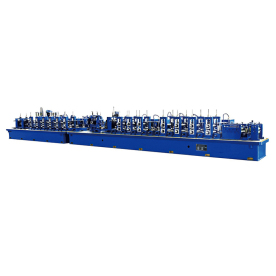
Exploring the Advantages and Applications of Portable High Frequency Welders for Efficient and Versatile Welding Solutions
Conclusion
As the world moves towards more efficient and effective manufacturing processes, the importance of portable high frequency welders cannot be overstated. Their mobility, precision, speed, and versatility make them an excellent choice for a wide range of applications across various industries. By investing in a portable high frequency welder, companies can not only enhance their operational capabilities but also improve the quality of their work. As technology in this field continues to advance, we can expect portable high frequency welders to play an increasingly central role in modern welding practices.