[Customized Mould for Tube Mill Components]Exploring the Benefits and Innovations of Customized Mould for Tube Mill Components in Enhancing Production Efficiency and Quality
News 2024-11-5
In the contemporary manufacturing landscape, particularly within the metalworking and fabrication sectors, innovation has become a cornerstone of competitive advantage. One of the critical areas witnessing substantial advancements is the development and utilization of customized moulds for tube mill components. These tailored moulds are not only pivotal to the production process but also play a crucial role in enhancing the overall efficiency, quality, and flexibility of manufacturing operations.
Customized moulds for tube mill components are specifically designed to meet the unique demands of tube manufacturing processes. Unlike standard moulds, customized options are created following the exact specifications and requirements of a particular application or production run. This bespoke approach ensures that manufacturers can produce tubes with the desired shapes, sizes, and physical properties, catering effectively to the diverse needs of various industries, including construction, automotive, aerospace, and energy.
One of the most significant advantages of using customized moulds in tube mills is the increased production efficiency. By designing moulds that are optimized for the specific materials and tube designs being produced, manufacturers can significantly reduce lead times and minimize waste. Customized moulds allow for quicker transitions between different production runs, thus enhancing flexibility. This enables manufacturers to respond rapidly to market demands and changes in consumer preferences, ensuring they can keep pace in a fast-evolving marketplace.
Moreover, the precise fit and dimensional accuracy offered by customized moulds lead to a marked improvement in product quality. In industries where precision is paramount, such as aerospace and medical device manufacturing, even the slightest variations can result in significant issues. Customized moulds help mitigate these risks by ensuring that tube components are produced with tight tolerances that align with stringent industry standards. This not only enhances the integrity and reliability of the final products but also reduces the likelihood of rework or scrap, translating to substantial cost savings for manufacturers.
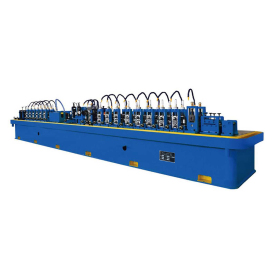
Exploring the Benefits and Innovations of Customized Mould for Tube Mill Components in Enhancing Production Efficiency and Quality
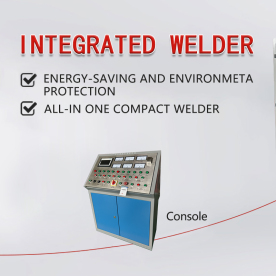
Exploring the Benefits and Innovations of Customized Mould for Tube Mill Components in Enhancing Production Efficiency and Quality
Another emerging trend is the integration of additive manufacturing, or 3D printing, in the production of customized moulds. This technology allows for the rapid prototyping of moulds, reducing the time and cost associated with traditional manufacturing methods. Additive manufacturing can produce intricate geometries that may be difficult or even impossible to achieve with conventional techniques. Consequently, this offers manufacturers unprecedented design freedom while also accelerating the time-to-market for new products.
Furthermore, the adoption of customized moulds also contributes to sustainable manufacturing practices. Customized moulds can be designed to optimize material usage, minimize waste, and enhance energy efficiency during the production process. As industries increasingly prioritize sustainability, the ability to produce high-quality tube components with reduced environmental impact becomes a significant selling point. Manufacturers embracing this approach can benefit from improved brand reputation and appeal to a growing segment of environmentally conscious consumers.
The evolution of customized moulds for tube mill components is also greatly impacted by the global push for automation and digitalization in manufacturing. The incorporation of smart technologies, such as the Internet of Things (IoT) and artificial intelligence (AI), into the design and functioning of moulds can lead to further enhancements in monitoring, maintenance, and operational efficiency. Real-time data analytics can provide manufacturers with insights into production performance, enabling them to anticipate potential issues and optimize operations proactively.
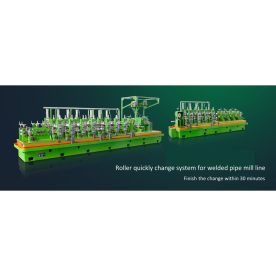