[High frequency welder machine]Understanding High Frequency Welder Machines: Their Application, Benefits, and Importance in Modern Manufacturing Processes
News 2024-10-31
****In today's fast-paced industrial world, the demand for precise and efficient welding processes has surged. As a result, high frequency welder machines have emerged as crucial tools in various sectors, including construction, automotive, aerospace, and manufacturing. These machines are designed to deliver high-quality welds through a process that utilizes high-frequency electrical currents to fuse materials together. In this article, we’ll delve into the intricacies of high frequency welder machines, exploring their applications, benefits, and why they are a vital component of modern manufacturing processes.
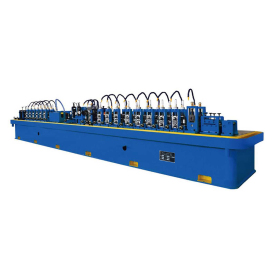
Understanding High Frequency Welder Machines: Their Application, Benefits, and Importance in Modern Manufacturing Processes
A high frequency welder machine is an advanced welding apparatus that employs high-frequency AC (Alternating Current) to produce heat, ultimately fusing materials. The machine operates by creating a high-frequency electromagnetic field, which induces molecular agitation in the materials being welded. This agitation generates heat, enabling the surfaces to melt and join together once adequate temperatures are reached. This efficient heating method is particularly effective for welding thin metals, plastics, and other materials that require precision.
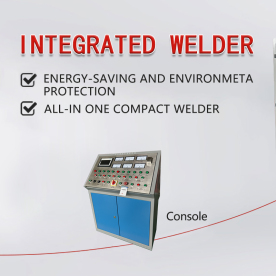
Understanding High Frequency Welder Machines: Their Application, Benefits, and Importance in Modern Manufacturing Processes
High frequency welder machines are versatile and can be applied across various industries:
1. **Plastics Manufacturing**: One of the most common applications is in the welding of plastic materials. Industries often utilize high frequency welding for producing items such as inflatable products, water bladders, and various automotive components. The process allows for strong welds without compromising the integrity of the surrounding material.
2. **Textile Industry**: In textiles, high frequency welders are essential for creating waterproof seams in outdoor gear, banners, and inflatable structures. The precise and clean welds ensure durability while maintaining a lightweight design.
3. **Automotive Sector**: Automotive manufacturers employ high frequency welding for assembling components such as fuel tanks and air ducts. The technique allows for joining different materials, including thermoplastics and elastomers, which are prevalent in the automotive industry.
4. **Aerospace Engineering**: The aerospace sector uses high frequency welding to achieve lightweight and strong joints in various structural components, demonstrating its importance in high-stakes applications where reliability is paramount.
5. **Electrical Components**: High frequency welders are also used in the manufacturing of electrical insulation materials, such as those found in transformers and capacitors, to create strong and effective components suitable for high-voltage applications.
Benefits of Using High Frequency Welder Machines
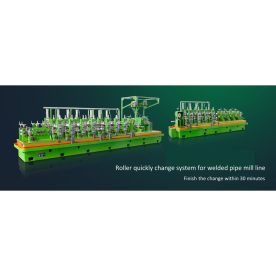
Understanding High Frequency Welder Machines: Their Application, Benefits, and Importance in Modern Manufacturing Processes
1. **Speed and Efficiency**: High frequency welding is fast, allowing manufacturers to increase production rates while maintaining quality. The quick heating process reduces cycle times significantly when compared to traditional welding methods.
2. **High-Quality Welds**: This technique produces strong, consistent welds with minimal heat-affected zones. As a result, the structural integrity of both welded materials is preserved, leading to durable end products.
3. **Energy Efficiency**: High frequency welder machines are designed to be energy efficient, using only the necessary power to achieve the desired results. This is particularly important for environmentally-conscious businesses looking to reduce their energy consumption.
4. **Versatility**: This technology can be adapted to weld a wide range of materials, including different types of plastics and metals. Such versatility makes it an invaluable asset across numerous industries.
5. **Reduced Manufacturing Costs**: Though the initial investment for high frequency welding equipment may be higher than conventional welding machines, the reduction in labor costs, maintenance, and energy consumption often leads to a lower overall expense in the long run.
Conclusion
High frequency welder machines represent a significant advancement in welding technology that meets the contemporary demands of various industries. Their ability to deliver fast, high-quality welds while being versatile and cost-effective solidifies their position as essential tools in today's manufacturing landscape. As industries continue to evolve with the integration of new materials and processes, high frequency welders will undoubtedly play a pivotal role in shaping the future of manufacturing efficiency and innovation.