[Durable Mould for Tube Mills]The Importance of Durable Mould for Tube Mills in Enhancing Production Efficiency and Product Quality
News 2024-10-31
In the world of manufacturing, particularly in the production of tubes and pipes, the quality and efficiency of the process can significantly impact the final product. One of the crucial elements in the production of tubes is the use of durable mould for tube mills. This article delves into the significance of durable moulds in tube mills, their applications, and the benefits they bring to the manufacturing process.
Tube mills are specialized machinery designed to produce pipes and tubes from various materials, including steel and aluminum. The molds used in these mills play a vital role in shaping the semi-finished products into the desired dimensions and specifications. A durable mould not only ensures the integrity of the product but also influences the overall production cycle, maintenance costs, and competitiveness of the manufacturing operation.
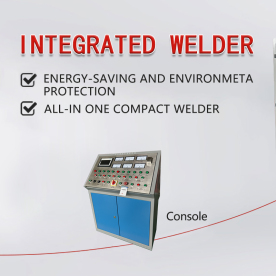
The Importance of Durable Mould for Tube Mills in Enhancing Production Efficiency and Product Quality
Moulds in tube mills serve to define the external and internal dimensions of the pipes produced. During the manufacturing process, sheets or strips of metal are fed into the tube mill, where they are formed into a cylindrical shape. The mould provides the necessary contour that gives the tube its specific diameter, wall thickness, and overall structural integrity. This shaping process is critical because even slight variations in the mould can lead to defects in the tube, rendering it unsuitable for its intended application.
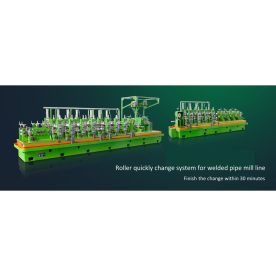
The Importance of Durable Mould for Tube Mills in Enhancing Production Efficiency and Product Quality
Advantages of Durable Moulds
One of the standout features of using durable moulds in tube manufacturing is their longevity. Durable moulds are typically constructed from high-quality materials designed to withstand the rigors of continuous manufacturing processes. This durability translates to longer service life and reduced downtime, as machinery operators do not need to replace or repair moulds as frequently. This aspect can lead to significant cost savings in the long run, as reduced maintenance also means less disruption to the production schedule.
Additionally, durable moulds exhibit better resistance to wear and tear, which enhances production quality. Wear and tear can lead to inaccuracies in the dimensions of the produced tubes, resulting in increased scrap rates and wasted material. With durable moulds, manufacturers can ensure consistent quality, leading to higher customer satisfaction and potentially less wasted resources.
High-quality moulds also contribute to improved heat dissipation during the production process. Excessive heat can negatively affect the material properties of the tubes being produced. Durable moulds, designed to handle high temperatures efficiently, help maintain the integrity of the materials, thus ensuring that the final product meets desired specifications without compromising strength or flexibility.
Customizability and Versatility
The ability to customize moulds further amplifies their importance in tube mills. Manufacturers can develop moulds tailored to their specific production requirements, allowing for greater flexibility in terms of the products that can be manufactured. As market demands shift and new industries emerge, having adaptable moulds can provide a competitive edge. Manufacturers may choose to invest in durable moulds that can accommodate a range of tube dimensions and types, making it easier to pivot in response to changes in demand.
Moreover, the versatility of durable moulds makes them valuable in various applications beyond the production of standard tubes. Specialized moulds enable manufacturers to create complex geometries and custom profiles, catering to industries such as automotive, aerospace, and construction, where unique tube designs are often required.

The Importance of Durable Mould for Tube Mills in Enhancing Production Efficiency and Product Quality
In conclusion, the significance of durable mould for tube mills cannot be overstated. These moulds enhance production efficiency, maintain product quality, and support cost-effective manufacturing operations. As manufacturers strive to meet increasing customer demands while remaining competitive, investing in high-quality, durable moulds becomes not just beneficial but essential. By choosing durable moulds, manufacturers position themselves to not only produce superior products but also to adapt to the changing landscape of the manufacturing industry, ensuring their continued success.