[Shear&butt welder]Exploring the Versatility and Applications of the Shear & Butt Welder in Modern Manufacturing
News 2024-10-31
In today’s fast-paced industrial world, the need for strong, durable, and precise welds has never been greater. Among the various welding technologies, the shear & butt welder stands out as a crucial tool in the manufacturing and fabrication sectors. This welding method, often employed in the production of metal parts and components, is known for its efficiency, reliability, and versatility. In this article, we will delve into the workings of the shear & butt welder, its applications, benefits, and how it compares to other welding techniques.
What is a Shear & Butt Welder?
A shear & butt welder is a specialized machine designed to join two pieces of metal together by applying heat and pressure. The process typically involves aligning the edges of the two materials to be welded, followed by applying a shear force while simultaneously heating the ends through resistance or other means. This method is particularly effective for connecting sheets of metal, pipes, and tubes, making it ideal for a variety of industries, including automotive, aerospace, and construction.
The shear & butt welding process can be broken down into a few key stages: alignment, heating, and joining. First, the components are accurately aligned to ensure the weld's integrity. The machine then applies heat to the edges of the materials. As the temperature rises, the material at the joint softens. Finally, a shear force is applied while keeping the materials in place, effectively fusing them together. Once the process is complete and the materials cool down, a strong bond is formed, resulting in a clean and robust weld.
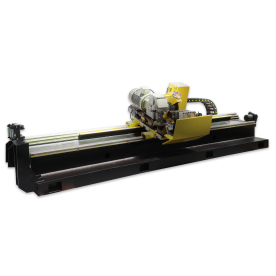
Exploring the Versatility and Applications of the Shear & Butt Welder in Modern Manufacturing
The versatility of shear & butt welders makes them suitable for various applications across multiple industries:
1. **Automotive Manufacturing**: In the automotive industry, shear & butt welders are used for assembling body parts, exhaust systems, and chassis components. The process allows for the joining of dissimilar materials, such as steel and aluminum, which is crucial for modern vehicle designs that prioritize weight reduction and fuel efficiency.
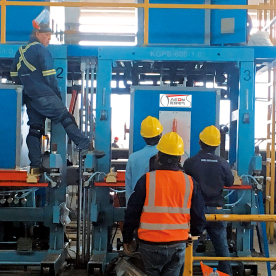
Exploring the Versatility and Applications of the Shear & Butt Welder in Modern Manufacturing
3. **Construction**: In the construction of buildings, bridges, and infrastructure, shear & butt welders help join structural steel elements. The efficiency of this method allows for quicker assembly times on large-scale projects, contributing to overall cost savings.
4. **Pipe and Tube Fabrication**: The ability to produce long runs of welded tubing and piping without the need for additional fitting makes shear & butt welders invaluable in industries such as oil and gas, water treatment, and chemical processing.
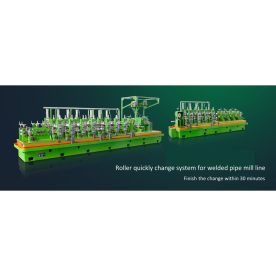
Exploring the Versatility and Applications of the Shear & Butt Welder in Modern Manufacturing
There are several advantages to using shear & butt welders in manufacturing processes:
- **Efficiency**: Shear & butt welding is a fast and continuous process, allowing for high production rates. This efficiency can significantly reduce labor costs and time associated with welding operations.
- **Quality Welds**: The precise control of the heat and pressure applied during the welding process results in high-quality welds with minimal defects. This reliability is crucial in industries where safety and structural integrity are paramount.
- **Reduced Need for Filler Materials**: Unlike some traditional welding methods that require additional filler materials, shear & butt welding can fuse materials together directly, which can save on costs and material waste.
- **Adaptability**: Shear & butt welders can be adapted for various materials and thicknesses, making them versatile tools in a diverse range of manufacturing settings.
Conclusion
In an era where efficiency, precision, and sustainability are key drivers in the manufacturing sector, the shear & butt welder has emerged as a crucial technology. Its ability to create strong, reliable welds across a variety of materials and applications has established it as a staple in modern industrial processes. As industries continue to evolve and necessitate more sophisticated solutions, shear & butt welders will undoubtedly play a significant role in shaping the future of manufacturing. Whether in automotive production lines, aerospace assembly, or construction projects, the shear & butt welder remains an indispensable tool in the quest for innovation and quality.