[Precision Mould for Tube Mills]Maximizing Efficiency in Tube Production: The Role of Precision Mould for Tube Mills
News 2024-10-30
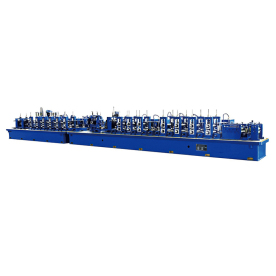
Maximizing Efficiency in Tube Production: The Role of Precision Mould for Tube Mills
In the highly competitive world of manufacturing, particularly in the tube production industry, maintaining high standards of precision and quality is paramount. Tube mills are essential equipment in the fabrication of steel and other materials into pipes and tubes for various applications. Among the innovations that have significantly advanced the capabilities of these tube mills is the use of precision mould tooling. Precision moulds enhance not only the efficiency of production processes but also the quality of the finished product, establishing themselves as a cornerstone in modern manufacturing.
Understanding Tube Mills
Tube mills are specifically designed for the rolling and forming of metal strips into tubes of various diameters and gauges. The process involves feeding a continuous strip of metal into the mill, which then shapes the strip into tubular forms through a series of rollers and dies. Traditional tube mills have inherent limitations regarding accuracy and the uniformity of the final product. This is where the integration of precision moulds makes a significant difference.
Importance of Precision Moulds
Precision moulds engineer specific shapes and dimensions, which are critical in achieving uniformity in tube production. By using precision moulds, manufacturers can reduce wastage and ensure that produced tubes meet strict industry specifications. Accurate moulds minimize discrepancies in tube thickness and ensure that the final products possess the required mechanical properties.
In the context of tube mills, precision mould technology provides several distinct advantages. First, they facilitate faster production speeds without compromising quality. With precision engineered to the tightest tolerances, tube mills equipped with high-quality moulds can operate efficiently, producing more tubes per hour and thereby increasing the overall throughput. This enhancement translates directly to reduced production costs and improved profitability for manufacturers.
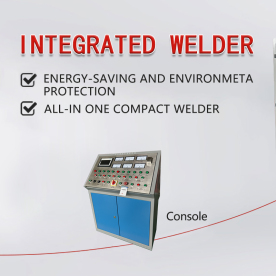
Maximizing Efficiency in Tube Production: The Role of Precision Mould for Tube Mills
1. **Quality Control**: Precision moulds are designed to produce tubes that meet exact specifications consistently. In industries where adherence to quality is non-negotiable—such as aerospace, automotive, and construction—integrating precision moulds into the tube manufacturing process ensures that products are reliable, durable, and safe.
2. **Reduced Material Waste**: When tube mills use precision moulds, they experience less material waste. By achieving precise dimensions on the first pass, manufacturers can rest assured that the raw materials are utilized effectively, which is especially beneficial given the rising costs of metals.
3. **Customization and Flexibility**: Advanced mould technologies allow manufacturers to customize the production of tubes to meet specific client needs without overhauling the entire production line. This flexibility is critical in a market that increasingly demands niche products.
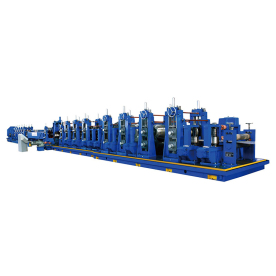
Maximizing Efficiency in Tube Production: The Role of Precision Mould for Tube Mills
5. **Advanced Technologies**: The incorporation of digital monitoring systems in conjunction with precision moulds allows manufacturers to track the performance of their tube mills in real-time. This data-driven approach enables on-the-fly adjustments, further enhancing operational efficiency.
Conclusion
In conclusion, the role of precision mould in tube mills cannot be overstated. As manufacturing demands evolve, and the market becomes ever more competitive, the integration of precision tooling becomes an absolute necessity. Whether it’s about enhancing the speed of production, maintaining stringent quality controls, or reducing waste and costs, precision moulds stand out as a vital component in the arsenal of modern tube manufacturers.
As the industry progresses, investing in state-of-the-art precision mould technologies will not only differentiate leading tube production companies but also ensure that they remain resilient against fluctuating market demands. Embracing innovations in precision engineering is the way forward for businesses aiming to thrive in today’s manufacturing landscape. Ultimately, precision moulds for tube mills will empower manufacturers to create products that not only meet but exceed customer expectations in quality and performance.