[High-efficiency All-in-one Welding System]Revolutionizing Metal Fabrication: The Advantages of a High-Efficiency All-in-One Welding System for Modern Industries
News 2024-10-30
In the ever-evolving landscape of industrial manufacturing and metal fabrication, the adoption of advanced technologies plays a crucial role in ensuring efficiency, safety, and cost-effectiveness. One of the most significant innovations in this arena is the High-efficiency All-in-one Welding System. This powerful tool not only simplifies the welding process but also enhances productivity and precision, making it an invaluable asset across various industries.
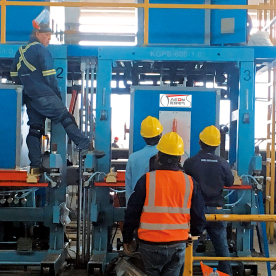
Revolutionizing Metal Fabrication: The Advantages of a High-Efficiency All-in-One Welding System for Modern Industries
A High-efficiency All-in-one Welding System combines multiple welding processes and technologies into one compact unit. These systems typically incorporate MIG welding, TIG welding, stick welding, and sometimes even flux-cored welding. The flexibility to switch between welding types allows users to tackle diverse projects without the need for multiple machines, reducing setup time and saving space in the workspace.
High-efficiency models are designed to optimize power consumption and enhance the quality of welds. Advanced inverter technology ensures that power usage is minimized while maintaining optimal welding performance, which translates into cost savings on energy bills. In an industry where profits can be razor-thin, these savings can make a significant difference to the bottom line.
Key Features and Benefits
1. **Versatility**: One of the primary advantages of a High-efficiency All-in-one Welding System is its versatility. Operators can seamlessly switch between different welding techniques, making it easier to handle varying materials and thicknesses. This flexibility enables manufacturers to take on a broader array of projects without investing in additional equipment.
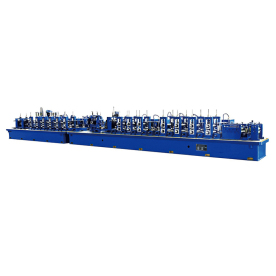
Revolutionizing Metal Fabrication: The Advantages of a High-Efficiency All-in-One Welding System for Modern Industries
3. **Increased Productivity**: High-efficiency welding systems are engineered to provide faster burn rates and shorter arc lengths without sacrificing weld quality. This boosts productivity, allowing teams to complete more projects in less time. Moreover, the reduced downtime associated with switching between machines can significantly enhance workflow efficiency.
4. **Quality and Consistency**: Advanced technology integrated into these welding systems minimizes human error, ensuring consistent and high-quality welds. Features like digital displays and automated settings allow operators to easily monitor and adjust parameters, leading to better results and fewer defects in the final product.
5. **User-Friendly**: Many high-efficiency models come equipped with intuitive control interfaces, making it easier for operators of all skill levels to use. Training new staff becomes less of an issue, as the user-friendly design allows for quicker onboarding and smoother transitions.
6. **Safety Enhancements**: Safety is always a concern in welding environments. Modern all-in-one systems include protective features such as thermal overload protection, automatic shutoff mechanisms, and improved ventilation to help keep both the operator and the workspace safe.
Applications in Various Industries
The High-efficiency All-in-one Welding System is applicable across a vast range of sectors, including automotive manufacturing, construction, shipbuilding, and pipeline welding. Each industry benefits from the adaptability, speed, and high-quality output that these systems provide. In automotive manufacturing, for example, the ability to weld both thin and thick materials quickly is highly desirable for meeting production deadlines.
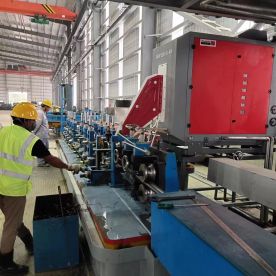
Revolutionizing Metal Fabrication: The Advantages of a High-Efficiency All-in-One Welding System for Modern Industries
Conclusion
As industries continue to shift towards automation and efficiency, the High-efficiency All-in-one Welding System stands out as a key player in the skilled trades. By providing versatility, improved performance, and substantial cost savings, these systems exemplify the best of modern welding technology. Embracing this innovative equipment can drive productivity and quality, setting the stage for success in an increasingly competitive global marketplace. Investing in a High-efficiency All-in-one Welding System may very well determine the future growth and sustainability of metal fabrication businesses in the years to come.