[Pipe mill production line]Enhancing Efficiency and Quality: A Comprehensive Guide to Pipe Mill Production Line Best Practices and Innovations
News 2024-10-30
Introduction
In the modern industrial landscape, the demand for high-quality pipes has surged, driven by advancements in construction, infrastructure development, and energy projects. At the heart of this growing demand lies the Pipe Mill Production Line— a complex system designed to manufacture pipes with precision and efficiency. This article explores the intricacies of the pipe mill production line, outlining its components, the latest innovations, and best practices to optimize production while maintaining quality.
Understanding the Pipe Mill Production Line
The pipe mill production line is a series of interconnected machines and processes that work together to transform raw materials into finished pipes. The primary goal of this production line is to produce piping products that meet stringent quality standards and specifications for various applications, including oil and gas, water, and construction.
Key Components of a Pipe Mill Production Line
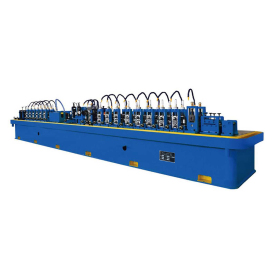
Enhancing Efficiency and Quality: A Comprehensive Guide to Pipe Mill Production Line Best Practices and Innovations
2. **Forming and Welding**: The next step involves forming the flat steel strips into a circular shape and welding the edges together. Various methods can be employed for this, including high-frequency electric resistance welding (ERW) and submerged arc welding (SAW). These techniques allow for the creation of strong, durable joints that are critical for pipe integrity.
3. **Heat Treatment and Sizing**: Post-welding, the pipes often undergo heat treatment to enhance mechanical properties. Afterward, the pipes are sized to ensure uniformity and adherence to the required dimensions. A sizing mill plays a vital role in this process, utilizing mandrels to achieve precise diameter and wall thickness.
4. **Finishing Operations**: Finishing procedures, including surface treatment and coating, follow the sizing process. These steps not only improve the aesthetic appeal of the pipes but also provide protection against corrosion and other environmental factors.
5. **Quality Control**: Throughout the production line, rigorous quality control measures are implemented to monitor the properties of the pipes. Non-destructive testing methods, such as ultrasonic and radiographic inspections, are commonly used to verify the integrity of welded seams and overall pipe quality.
Innovations Impacting Pipe Mill Production Lines
The pipe manufacturing industry is continually evolving, with innovations emerging to enhance production efficiency and product quality. Several noteworthy advancements include:
1. **Automation and Smart Technologies**: Integrating IoT (Internet of Things) and AI (Artificial Intelligence) into production lines has revolutionized the pipe manufacturing process. Smart sensors monitor equipment performance in real-time, allowing for predictive maintenance and minimizing downtime. Moreover, automated systems streamline workflows, reduce human error, and ensure consistent quality.
2. **Advanced Welding Techniques**: The introduction of laser welding technology has transformed the welding process, producing stronger and more precise joints. This method minimizes heat input, reducing the risk of warping and enhancing overall pipe strength.
3. **Sustainable Practices**: The growing emphasis on sustainability has prompted pipe manufacturers to adopt eco-friendly practices. Utilizing recycled materials, implementing energy-efficient machines, and reducing waste during production have become standard practices in modern pipe mills.
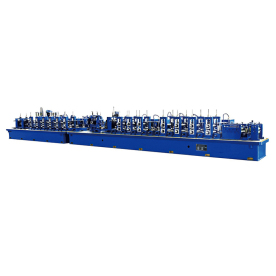
Enhancing Efficiency and Quality: A Comprehensive Guide to Pipe Mill Production Line Best Practices and Innovations
To maximize efficiency and product quality in pipe manufacturing, several best practices should be considered:
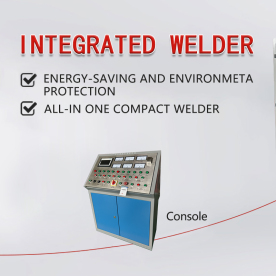
Enhancing Efficiency and Quality: A Comprehensive Guide to Pipe Mill Production Line Best Practices and Innovations
2. **Employee Training and Development**: Investing in employee training fosters a skilled workforce that can operate machinery effectively and respond to production challenges. Continuous learning opportunities also keep staff informed about new technologies and techniques.
3. **Data-Driven Decision Making**: Leveraging data analytics tools can provide insights into production performance, helping management identify bottlenecks, inefficiencies, and opportunities for improvement.
Conclusion
The Pipe Mill Production Line is an integral component of the manufacturing ecosystem, catering to the increasing global demand for pipes. By understanding its complexities and adopting innovative practices and technologies, manufacturers can enhance both efficiency and product quality. As the industry continues to evolve, staying ahead of technological advancements and implementing best practices will be crucial for maintaining a competitive edge in this dynamic market.