[Tube making machine]Understanding the Mechanics and Innovations Behind Modern Tube Making Machines for Efficient Production
News 2024-10-26
****In today’s manufacturing landscape, the demand for precision engineering and efficient production processes has drastically increased. One of the unsung heroes of modern production lines is the tube making machine. These machines specialize in creating tubes and pipes of various materials and sizes, catering to industries ranging from construction to automotive and beyond. This article delves into the mechanics of tube making machines, their applications, advancements in technology, and the future of this essential manufacturing equipment.
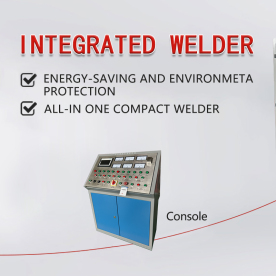
Understanding the Mechanics and Innovations Behind Modern Tube Making Machines for Efficient Production
A tube making machine is a sophisticated piece of machinery that fabricates tubes from raw materials, which can include metals, plastics, and composites. The process typically involves several stages, including forming, welding, cutting, and finishing. The types of tubes produced can vary widely, including round, square, and rectangular shapes, as well as specific designs for different applications.
The Tube Manufacturing Process
The process generally begins with the selection of the raw material, which is usually fed into the machine in coil form. The machine then employs several mechanical and thermal processes to transform this material into the desired tube shape. The primary steps involved in the tube manufacturing process include:
1. **Material Preparation**: The raw material, often a flat metal sheet or coil, is prepared for processing. This stage may involve cleaning, straightening, and cutting to size.
2. **Forming**: The flat material is then passed through forming rollers that bend it into a cylindrical shape. Depending on the machine, different forming techniques may be used, including incremental forming or roll forming.
3. **Welding**: Once the material is shaped, the edges are welded together to create a continuous tube. This welding can be achieved using various techniques such as High-Frequency Electric Resistance Welding (HFERW), Laser welding, or Tungsten Inert Gas (TIG) welding.
4. **Cutting**: The continuous tube is then cut to the desired length. This can be accomplished with saws or other cutting devices, often integrated into the machine itself.
5. **Finishing**: The final step involves any additional processes such as deburring, polishing, or applying coatings to enhance the tube's performance characteristics.
Applications of Tube Making Machines
Tube making machines are used across an array of industries due to their versatility. Here are some of the sectors that heavily rely on tube manufacturing:
- **Construction Industry**: Steel and aluminum tubes are extensively used in structural applications, scaffolding, and supports. - **Automotive Manufacturing**: Tubes are critical components in car frames, exhaust systems, and fuel lines. - **Consumer Products**: These machines also produce tubes used in consumer goods, such as toothpaste, cosmetics, and food packaging. - **Energy Sector**: Tubes are essential for pipelines in oil and gas operations, as well as in renewable energy installations.
Technological Advancements in Tube Making Machines
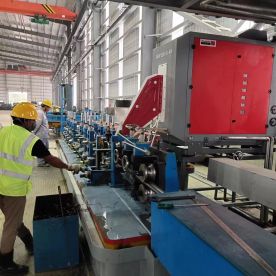
Understanding the Mechanics and Innovations Behind Modern Tube Making Machines for Efficient Production
- **Automation**: Many machines now incorporate automation technologies, reducing the need for manual labor, increasing precision, and allowing for real-time monitoring and adjustments. - **Computer Numerical Control (CNC)**: CNC technology allows for highly precise machining processes, enabling manufacturers to produce complex designs with tight tolerances. - **Energy Efficiency**: Newer tube making machines are designed to consume less energy, employing systems that optimize energy use during the manufacturing process, thereby reducing costs and ecological impact.
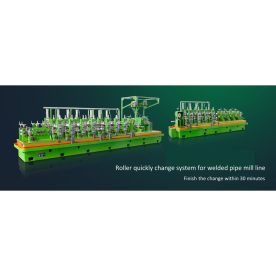
Understanding the Mechanics and Innovations Behind Modern Tube Making Machines for Efficient Production
Looking ahead, the future of tube making machinery seems promising. Advances in materials science may lead to the creation of lighter and stronger materials, which will affect tube design and functionality. Furthermore, developments in digital technology could pave the way for more interconnected and smart manufacturing systems, enhancing inventory management, production scheduling, and real-time adjustments.
In conclusion, the tube making machine is a formidable piece of equipment that is integral to many industries. Understanding its function, applications, and advancements is essential for manufacturers seeking efficiency and innovation. As technology continues to progress, the capabilities of tube making machines will undoubtedly enhance, setting new standards in the world of manufacturing.