[Solid state high frequency welder machine]Exploring the Innovations and Applications of Solid State High Frequency Welder Machines in Modern Manufacturing and Industry
News 2024-10-22
****In the competitive landscape of modern manufacturing, the quest for efficient, reliable, and precise welding techniques has led to the advent of advanced technologies. Among these innovations, the solid state high frequency welder machine is gaining prominence due to its distinctive advantages, which include enhanced precision, reduced cycle times, and the capability to weld a variety of materials. This article delves into the workings of solid state high frequency welders, their applications, and the benefits they bring to various sectors.
Understanding Solid State High Frequency Welders
Solid state high frequency welders employ high-frequency electrical currents to generate heat within materials, enabling them to bond together without the need for additional filler materials. The key component of these machines is their solid-state circuitry, which replaces traditional vacuum tubes, resulting in a more efficient and compact design. This innovation allows for rapid heating and improved control over the welding process, leading to higher quality welds and greater energy savings.
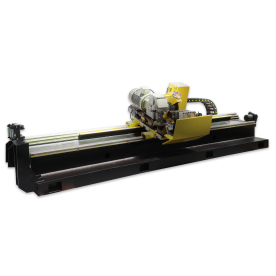
Exploring the Innovations and Applications of Solid State High Frequency Welder Machines in Modern Manufacturing and Industry
Applications in Various Industries
1. **Automotive Manufacturing**: In the automotive sector, solid state high frequency welders are used to bond thin metal sheets, such as those used in car body panels. The precise control of the welding process minimizes distortion and ensures that the materials retain their structural integrity.
2. **Electronics**: The electronics industry benefits significantly from solid state welding technology. These machines can weld delicate components such as lead wires and connectors with extreme accuracy, which is essential for maintaining the functionality and reliability of electronic devices.
3. **Aerospace**: Aerospace applications require the highest levels of quality and durability in welding processes. Solid state high frequency welders provide precise welds that meet stringent industry standards for safety and performance.
4. **Medical Devices**: In the medical field, the creation of devices often involves welding small, intricate components. The precision supplied by solid state high frequency welders ensures that these critical components are securely bonded without damaging the underlying materials.
5. **Textile and Fabric Industry**: Additionally, solid state welders are increasingly adopted in the textile industry for the production of high-frequency welded seams in fabrics, particularly in products like inflatable structures, tents, or protective gear.
Key Benefits of Solid State High Frequency Welders
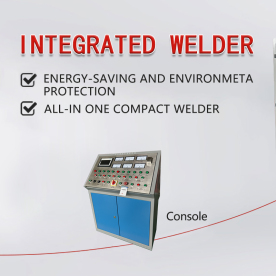
Exploring the Innovations and Applications of Solid State High Frequency Welder Machines in Modern Manufacturing and Industry

Exploring the Innovations and Applications of Solid State High Frequency Welder Machines in Modern Manufacturing and Industry
2. **Energy Savings**: The advanced technology in solid state welders allows for decreased energy consumption compared to traditional welding methods. This not only lowers operational costs but also makes the process more environmentally friendly.
3. **Versatility**: Solid state welders can be adjusted quickly for different materials and thicknesses, making them suitable for a wide range of applications. This versatility is crucial in dynamic manufacturing environments where product lines frequently change.
4. **Precision Control**: These machines offer superior control over the welding parameters, such as frequency and temperature, leading to high-quality welds with minimal defects.
5. **Reduced Maintenance**: The solid-state design means fewer moving parts and less wear and tear, resulting in lower maintenance needs and reduced downtime.
Conclusion
As industries continue to evolve and adapt to new challenges, the solid state high frequency welder machine stands out as a transformative technology that meets the demands for efficiency, precision, and flexibility. With applications spanning multiple sectors, it is clear that these machines are not just a trend, but rather a fundamental shift in how welding can enhance manufacturing processes. The future of welding lies in solid state technology, ensuring improved product quality and operational efficiency in various industries. As manufacturers embrace this innovative approach, the potential for higher performance and better sustainability in production processes will undoubtedly continue to grow.