[Tailor-Made Spare Parts for Tube Mills]Why Tailor-Made Spare Parts for Tube Mills are Essential for Maximizing Productivity and Minimizing Downtime in Manufacturing Facilities
News 2024-10-21
****In the realm of manufacturing, particularly in industries reliant on tube mills, the importance of maintaining optimal operational efficiency cannot be overstated. Tube mills, integral for producing various tubular products, require precision engineering and consistent maintenance to avoid costly downtimes. One effective solution to achieve this efficiency is the implementation of tailor-made spare parts designed specifically for the operational nuances of each tube mill.
**Understanding Tube Mills and Their Importance**
Tube mills are specialized machinery used for fabricating metal tubes and pipes from sheet or strip metal. These mills are used in various sectors, including construction, automotive, aerospace, and energy. Given their diverse applications, any inefficiency or breakdown can lead to significant delays, increased operational costs, and a decline in product quality.
With the rising demand for specialized and high-quality tubes, manufacturers are pressed to maintain their tube mills in peak condition. Standard off-the-shelf components might not always meet the unique requirements of different tube mill models or production setups. This is where the importance of tailor-made spare parts comes into play.
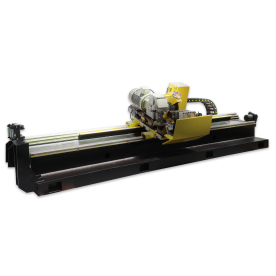
Why Tailor-Made Spare Parts for Tube Mills are Essential for Maximizing Productivity and Minimizing Downtime in Manufacturing Facilities
Tailor-made spare parts offer several advantages over generic alternatives. Firstly, they are designed to fit the specific dimensions and performance characteristics of a particular tube mill, ensuring that the components work seamlessly together. This not only helps in maintaining the integrity of the machinery but also enhances the overall efficiency of the production line.
Furthermore, tailor-made parts can be engineered to handle specific operational conditions, such as varying temperatures, pressures, and material types. For example, when producing thicker or more durable tubes, standard parts may fail under increased stress, leading to premature wear or breakage. Custom-engineered spare parts ensure longevity and resilience, minimizing the risk of unexpected failures.
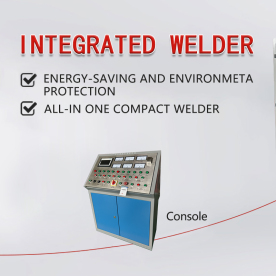
Why Tailor-Made Spare Parts for Tube Mills are Essential for Maximizing Productivity and Minimizing Downtime in Manufacturing Facilities
One of the most significant benefits of tailor-made spare parts is the positive impact on productivity. When parts are specifically made for a tube mill, they are less likely to malfunction. As a result, manufacturers can keep their production lines running smoothly, thus reducing the frequency and duration of unscheduled maintenance. This directly translates to increased output and profitability.
Moreover, having a stock of tailor-made spare parts readily available can drastically reduce lead times. Unlike standard parts that may require lengthy shipping times or back orders, custom parts can be produced in anticipation of future needs. Manufacturers can avoid the stress of sudden breakdowns, which can derail production schedules and lead to missed deadlines.
**Economical Considerations**
Though custom parts may initially appear to be a more substantial economic investment than off-the-shelf alternatives, they often provide long-term savings. The higher durability and better fit of tailor-made spare parts reduce the frequency of replacements and repairs, ultimately translating into lower operational costs. Additionally, the improved efficiency provided by these parts can lead to faster production cycles, contributing to increased revenue.
By investing in tailor-made solutions, manufacturers can also reduce the amount of energy required for operation. When spare parts fit properly and operate efficiently, energy consumption decreases, resulting in lower utility bills. This approach aligns well with the increasing focus on sustainability within manufacturing.
**Partnership with Experts**

Why Tailor-Made Spare Parts for Tube Mills are Essential for Maximizing Productivity and Minimizing Downtime in Manufacturing Facilities
Additionally, staying updated with the latest innovations in materials and manufacturing techniques can further enhance performance and reliability. A good manufacturer-client relationship can foster continual improvement and adaptation to the ever-evolving market dynamics.
**Conclusion**
In conclusion, the case for tailor-made spare parts for tube mills is compelling. By investing in custom-engineered components, manufacturers can maximize productivity and minimize downtime while achieving cost savings in the long run. In a competitive marketplace, such strategic moves are essential for ensuring operational success and sustainability. Embracing tailor-made solutions not only enhances the efficiency of tube mills but also ensures that businesses remain resilient and responsive to market demands.