[Precision Tube making equipment]Exploring the Advancements in Precision Tube Making Equipment: Revolutionizing Industries with Enhanced Accuracy and Efficiency
News 2024-10-21
****In the modern manufacturing landscape, precision is paramount. Across various industries—from aerospace and automotive to medical devices and electronics—the need for precision-engineered parts has skyrocketed. One of the significant players in this evolution is precision tube making equipment, which has undergone remarkable advancements to meet the growing demands for accuracy, efficiency, and versatility.
Precision tube making equipment encompasses a wide range of machines and technologies used to produce tubular components with tight tolerances and specific physical properties. Recent innovations in this field have not only improved production capabilities but have also broadened the spectrum of applications for these tubes. The performance of precision tube making equipment can dramatically impact the end product's quality and reliability, which is especially crucial in sectors where safety and performance are non-negotiable.
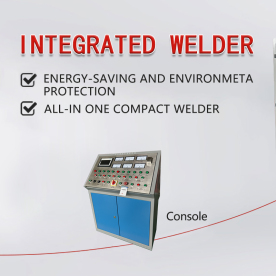
Exploring the Advancements in Precision Tube Making Equipment: Revolutionizing Industries with Enhanced Accuracy and Efficiency
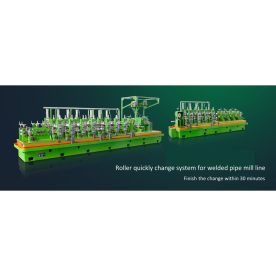
Exploring the Advancements in Precision Tube Making Equipment: Revolutionizing Industries with Enhanced Accuracy and Efficiency
Furthermore, the advent of computer numerical control (CNC) technology has transformed precision tube manufacturing. CNC machines enable manufacturers to produce complex shapes and sizes that were previously unachievable with conventional methods. The precision achieved through CNC machining allows for the production of intricate designs, such as those required in the medical industry for catheters or surgical instruments. Additionally, the repeatability of CNC processes means that manufacturers can produce large volumes of parts with consistent quality, significantly reducing waste and rework costs.
Materials play a crucial role in the effectiveness of precision tube making equipment. Manufacturers are increasingly looking towards high-performance alloys and composites to enhance the mechanical properties of their tubes. With improved materials, manufacturers can create tubes that not only meet strict industry standards but also last longer and perform better under extreme conditions. The introduction of additive manufacturing, or 3D printing, is another exciting development in the arena of precision tubes. This technology allows for the creation of complex geometries from a wide range of materials, providing designers with unprecedented freedom while ensuring that the quality of the tubes remains consistently high.

Exploring the Advancements in Precision Tube Making Equipment: Revolutionizing Industries with Enhanced Accuracy and Efficiency
Operational efficiency has become a key focus in the development of precision tube making equipment. Equipment equipped with real-time monitoring capabilities allows manufacturers to gather data on machine performance, detect issues before they escalate, and implement preventive maintenance to avoid downtime. This capability not only enhances productivity but also contributes to overall cost savings. Manufacturers can maintain a continuous production flow, ensuring timely delivery of high-quality products to customers.
As industries evolve, the demands on precision tube making equipment will continue to grow. Manufacturers must stay ahead of the curve by embracing emerging technologies, optimizing existing processes, and maintaining flexibility in their operations. This adaptability will be critical in catering to the increasingly specialized needs of diverse industries, from aerospace with its stringent safety protocols to the ever-advancing medical sector seeking innovative treatments.
In conclusion, the realm of precision tube making equipment is at the forefront of manufacturing innovations, offering unprecedented accuracy, efficiency, and sustainability. As businesses look for ways to enhance their production processes, precision tube making equipment will play a vital role in shaping the future of efficient manufacturing. The ongoing advancements in this field not only promise to revolutionize industries but also ensure that manufacturers can meet the rigorous demands of quality and performance expected by their customers in the years to come.