[Solid state HF welder for thin metal sheets]Introducing the Solid State HF Welder: The Game-Changer for Joining Thin Metal Sheets Efficiently and Effectively
News 2024-10-19
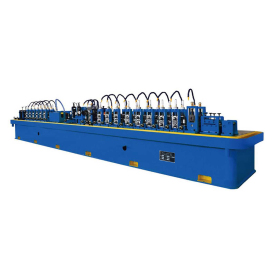
Introducing the Solid State HF Welder: The Game-Changer for Joining Thin Metal Sheets Efficiently and Effectively
The Mechanism Behind Solid State HF Welding
Solid state HF welding is a process that utilizes high-frequency electrical signals to generate heat within the metal sheets being joined. Unlike traditional welding methods, which often rely on high temperatures created by external flames or arcs, solid state HF welding offers a more controlled and efficient approach. The key aspect of this technology is its ability to create molecular bonds at a localized area of the metal sheets without significantly affecting their overall properties.
In a solid-state HF welder, high-frequency generators send electrical currents through specific parts of the metal sheets. The high electrical resistance at the interface creates localized heating, causing the metal to reach its melting point quickly. As the materials cool, they fuse together to form a strong bond. This process can be used on various metal materials, including stainless steel, copper, aluminum, and more.
Advantages of Solid State HF Welders for Thin Metal Sheets
1. **Precision and Control**: One of the standout features of solid-state HF welders is their ability to provide precise control over the welding process. Users can adjust parameters such as frequency, voltage, and power to optimize the weld quality according to the metal type and thickness. This is particularly beneficial when working with thin metal sheets, where excessive heat can warp or damage the material.
2. **High Speed**: Solid state HF welding is known for its speed. The process minimizes heating time and enables quick transitions between different welding spots, which is essential in high-volume production where time is of the essence. This efficiency helps companies meet tight production deadlines without compromising on quality.
3. **Reduced Material Distortion**: By limiting the heat affected zone (HAZ), solid state HF welding significantly reduces distortion and warping that are commonly associated with traditional welding processes. This characteristic is especially critical when dealing with thin metal sheets, where maintaining dimensional accuracy is essential for the final product.
4. **Energy Efficiency**: Compared to traditional welding techniques, solid-state HF welding consumes less energy. This not only results in lower operational costs but also aligns with the growing push for environmentally friendly manufacturing practices.
5. **Versatile Applications**: Solid state HF welders are suitable for a wide range of applications in various industries, including automotive, aerospace, electronics, and construction. This versatility makes them an attractive option for manufacturers who need to work with different metal compositions and thicknesses.
Applications in Different Industries
The utility of solid state HF welders extends into numerous sectors, each benefiting from the ability to rapidly and accurately join thin metal sheets. In the automotive industry, for example, these welders are often employed to create lightweight components that enhance fuel efficiency while maintaining structural integrity.
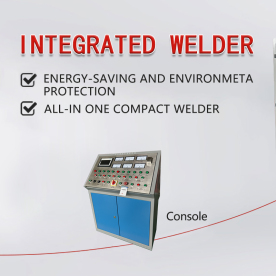
Introducing the Solid State HF Welder: The Game-Changer for Joining Thin Metal Sheets Efficiently and Effectively
Similarly, electronics manufacturers utilize this technology to assemble delicate components where precision is paramount. In construction, solid state HF welding can be used in the creation of metal curtain walls and other structures requiring lightweight yet durable materials.
Conclusion
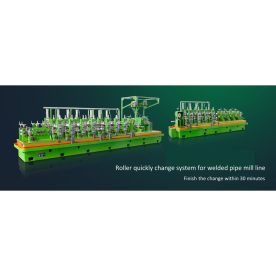