[Durable Mould for Tube Mills]Exploring the Advantages of Using Durable Mould for Tube Mills in Enhancing Production Efficiency and Product Quality
News 2024-10-19
****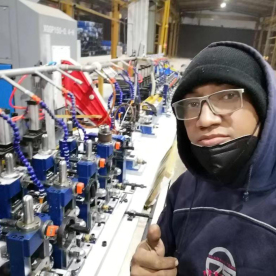
Exploring the Advantages of Using Durable Mould for Tube Mills in Enhancing Production Efficiency and Product Quality
What Are Tube Mills?
Tube mills are specialized machines designed to form and produce tubular products from metal strips or coils. These mills utilize a series of roll stands that progressively shape the material into the desired tube or pipe configuration. Tube mills are employed across various industries, including construction, automotive, aerospace, and oil and gas, making them foundational to modern manufacturing.
The Role of Moulds in Tube Mills
Moulds, or dies, in tube mills act as the guiding and shaping mechanisms that determine the final dimensions and quality of the product. They ensure that metal strips are consistently formed into precise lengths, diameters, and wall thicknesses. The durability of these moulds is critical, as they are subjected to high pressures, temperatures, and wear during the milling process. This is where the concept of durable moulds becomes particularly important, offering numerous benefits over traditional mould materials.
Advantages of Durable Mould for Tube Mills
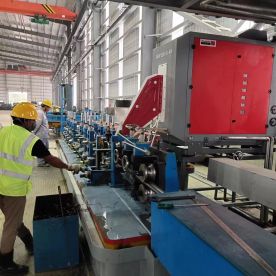
Exploring the Advantages of Using Durable Mould for Tube Mills in Enhancing Production Efficiency and Product Quality
2. **Improved Precision**: The manufacturing of tubular products demands a high degree of accuracy. Durable moulds maintain their shape and dimensional integrity over time, ensuring that the products produced meet stringent quality standards. This translates to better fit and performance in applications, particularly in industries where precision is non-negotiable.
3. **Cost-Effectiveness**: While the initial investment in durable moulds may be higher, the long-term savings realized through reduced maintenance, less frequent replacements, and decreased production errors can significantly outweigh the costs. Companies can experience enhanced profitability as a result of these efficiencies.
4. **Increased Production Rates**: With durable moulds capable of withstanding higher operational stresses, tube mills can often run at faster production rates without compromising quality. This increase in throughput helps manufacturers meet market demands without sacrificing performance.
5. **Versatility in Application**: Durable moulds can accommodate various materials, including high-strength steels and exotic alloys, allowing manufacturers the flexibility to expand their product offerings and explore new markets.
6. **Reduced Energy Consumption**: Efficient mould designs can lead to optimized energy use during the milling process. Durable moulds can minimize friction and enhance the flow of materials, translating to lower energy costs and a reduced carbon footprint for the manufacturing operation.
Conclusion
The integration of durable moulds in tube mills represents a significant advance in manufacturing technology. As industries continue to evolve and place greater demands on production processes, the ability to produce high-quality, precise tubular products efficiently becomes paramount. Durable moulds provide an ideal solution, combining longevity, precision, and cost-effectiveness.
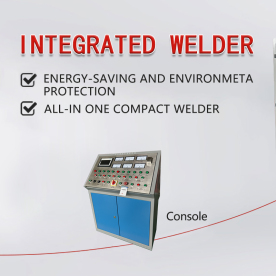