[Durable Mould for Tube Mills]Enhancing Production Efficiency with Durable Mould for Tube Mills: Maximizing Output and Minimizing Downtime
News 2024-10-18
****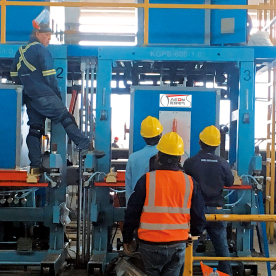
Enhancing Production Efficiency with Durable Mould for Tube Mills: Maximizing Output and Minimizing Downtime
The Role of Moulds in Tube Mills
At the core of any tube mill lies the mould system, which shapes and guides the raw material through the process of forming tubes. The precision of these moulds directly impacts the dimensional accuracy and surface quality of the finished product. In tube mills, moulds must withstand high degrees of wear and thermal shock, especially given the heavy-duty nature of the operations involved. Therefore, investing in durable mould technology is of paramount importance for manufacturers aiming to maintain high standards of quality while optimizing their production processes.
Durability: A Key Factor
Durability in moulds refers to their ability to resist wear, deformation, and failure over time. The harsh environment within a tube mill, characterized by high speeds, pressure, and varying temperatures, necessitates moulds that can endure these conditions without compromising their performance. Durable moulds are typically fabricated from high-grade materials, such as tool steel or specialized alloys, that are designed to withstand the rigors of continuous operation.
When moulds are constructed with durability in mind, they require less frequent replacements or repairs. This translates to fewer interruptions in production, lower maintenance costs, and an overall increase in output efficiency. Furthermore, high-quality moulds contribute to the uniformity and consistency of the product, minimizing defects that could lead to product rejections or returns.
Benefits of Using Durable Moulds
1. **Enhanced Production Efficiency**: Durable moulds facilitate a smoother production process, allowing tube mills to operate at higher speeds without the risk of breakdown or quality loss. This efficiency is crucial in meeting market demands and maintaining a competitive edge.
2. **Reduced Downtime**: Frequent breakdowns and mould replacements can significantly hamper the overall productivity of tube mills. By investing in durable moulds, manufacturers can experience decreased downtime, as fewer repairs and replacements will be necessary. This level of reliability ensures that production schedules are met consistently.
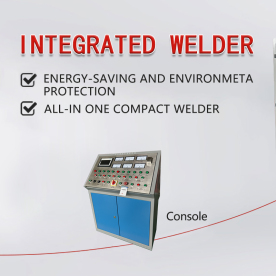
Enhancing Production Efficiency with Durable Mould for Tube Mills: Maximizing Output and Minimizing Downtime
4. **Improved Product Quality**: The quality of the final product is paramount in the tube manufacturing industry. Durable moulds maintain precision throughout the production process, leading to better dimensional accuracy and enhanced surface finishes. This focus on quality can strengthen customer relationships and bolster a company’s reputation.
5. **Sustainability**: With environmental concerns at the forefront of modern manufacturing, durable moulds align with sustainability goals. By reducing waste through lower replacement rates and minimizing energy consumption due to efficient operations, manufacturers can adopt greener practices.
Choosing the Right Durable Mould
When selecting durable moulds for tube mills, manufacturers need to consider several factors, including the type of material being processed, the specific design requirements, and the production line’s operational speed. Collaborating with suppliers who specialize in high-performance mould technology can ensure that the right solutions are implemented. Customization options may also be available, allowing companies to tailor moulds to their specific needs.
Conclusion
