[Tube mill production line]Understanding the Tube Mill Production Line: Key Processes, Benefits, and Applications in Modern Manufacturing
News 2024-10-18
****In the world of manufacturing, the tube mill production line plays a crucial role in the creation of seamless and welded tubes. This sophisticated assembly line is not only pivotal for producing high-quality tubes but also significantly enhances operational efficiency in various industries. By exploring the fundamental processes, benefits, and applications of tube mill production lines, we can appreciate their importance in contemporary manufacturing.
**What is a Tube Mill Production Line?**
At its core, a tube mill production line comprises a series of machines and equipment designed to manufacture tubes from metal strip or sheet material. The production line can be customized to produce different types and sizes of tubes, including round, square, and rectangular shapes.
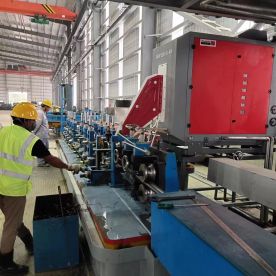
Understanding the Tube Mill Production Line: Key Processes, Benefits, and Applications in Modern Manufacturing
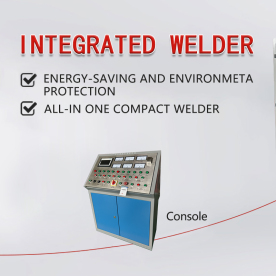
Understanding the Tube Mill Production Line: Key Processes, Benefits, and Applications in Modern Manufacturing
1. **Uncoiling and Straightening:** The production line begins with coiled metal strips that are unwound and straightened. This step is crucial for preparing the base material for the subsequent stages of tube manufacturing.
2. **Forming:** In this step, the flat strip is rolled and shaped into a tube. Depending on the desired shape—whether round, square, or rectangular—specific forming machines are used. This process often involves multiple sets of rollers that gradually bend the strip into the desired form.
3. **Welding:** Once the metal strip is formed into a tube, the edges are brought together and welded. This is typically done using high-frequency induction welding, which is an efficient method that ensures strong and uniform seams. The welding process is critical, as it dictates the structural integrity of the final product.
4. **Sizing and Cooling:** After welding, the tube is resized as necessary to meet specific dimensional requirements. Cooling systems are often employed to stabilize the tube and prevent warping.
5. **Inspection and Testing:** Quality control is an integral part of the tube mill production line. Tubes undergo rigorous inspection and testing to ensure they meet industry standards. This can include non-destructive testing methods to detect any internal defects.
6. **Cutting and Finishing:** The final steps involve cutting the completed tubes to specified lengths and applying any finishing treatments, such as coating or polishing, to enhance corrosion resistance and aesthetics.
**Benefits of Tube Mill Production Lines**
The advantages of using a tube mill production line are manifold. Here are some key benefits:
1. **High Efficiency and Output:** Tube mill production lines are designed for high-speed manufacturing, which allows businesses to meet large orders and reduce lead times.
2. **Quality Assurance:** Automated processes reduce human error and ensure consistency in product quality. This is crucial for industries where precision is paramount, such as automotive and construction.
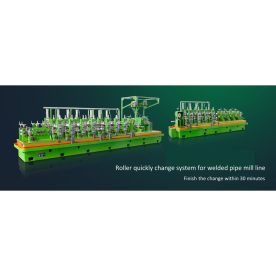
Understanding the Tube Mill Production Line: Key Processes, Benefits, and Applications in Modern Manufacturing
4. **Cost-Effective:** Although the initial investment in a tube mill production line can be significant, the long-term savings resulting from increased production efficiency, reduced labor costs, and lower material waste often outweigh this cost.
5. **Sustainability:** As industries increasingly focus on sustainability, tube mills can produce tubes from recycled materials, further reducing their environmental footprint.
**Applications of Tube Mill Production Lines**
Tube mill production lines are vital in several industries, including:
- **Construction:** Used for structural purposes, such as scaffolding and framing material. - **Automotive:** Essential for producing exhaust systems, chassis components, and other vital car parts. - **Oil and Gas:** Necessary for transporting materials and fluids through pipelines. - **Appliances:** Commonly found in HVAC systems and various household appliances.
In conclusion, the tube mill production line represents a cornerstone of modern manufacturing, encapsulating efficiency, quality, and versatility. As industries evolve and demand increases, the continued advancement of tube mill technology will play a significant role in meeting the manufacturing needs of the future. Understanding these processes and their applications helps businesses to appreciate the value of investing in such production lines, ensuring they remain competitive in a rapidly changing marketplace.