[High frequency welder equipment]The Importance of High Frequency Welder Equipment in Modern Manufacturing: Enhancing Precision and Efficiency in Welding Processes
News 2024-10-17
In the competitive landscape of modern manufacturing, the demand for precision, efficiency, and durability in welding processes has grown exponentially. One of the key innovations that have helped meet these demands is high frequency welder equipment. This advanced technology has transformed traditional welding methods, allowing industries to achieve higher-quality welds, reduce production times, and save costs. In this article, we will explore the significance, applications, and advantages of high frequency welder equipment in various sectors.
**Understanding High Frequency Welding**
High frequency welding, often referred to as HF welding, utilizes electromagnetic energy to create heat and fuse materials together. This method is particularly effective for welding thermoplastics and metals, making it widely used in industries such as automotive, aerospace, packaging, and textiles. Unlike traditional welding techniques that rely heavily on heat generated from an electric arc, high frequency welding produces heat quickly and efficiently through the dielectric heating process.
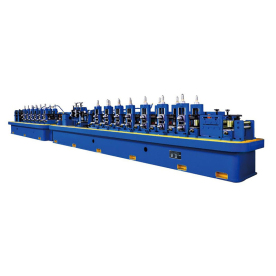
The Importance of High Frequency Welder Equipment in Modern Manufacturing: Enhancing Precision and Efficiency in Welding Processes
**Applications of High Frequency Welder Equipment**
High frequency welder equipment is versatile and can be used in numerous applications across various industries. Some of the most common applications include:
1. **Plastic Fabrication:** HF welding is widely used for fabricating plastic products, such as inflatable items, tarpaulins, and medical bags. The ability to create strong seams without compromising the integrity of the materials makes it an ideal choice for manufacturers in the packaging and medical sectors.
2. **Automotive Industry:** The automotive sector increasingly relies on high frequency welding for a variety of components, including dashboard assemblies, vinyl parts, and weatherstripping. The technology allows for high-speed welding, which is essential in meeting the demands of mass production.
3. **Aerospace Components:** In aerospace manufacturing, the need for lightweight and durable materials is paramount. High frequency welding enables the bonding of advanced composite materials and produces reliable joints that can withstand the rigors of flight.
4. **Textiles:** High frequency welder equipment is also utilized in the production of synthetic fabrics, where it is used to create durable seams and seals that provide both strength and water resistance.
**Advantages of High Frequency Welder Equipment**
The adoption of high frequency welder equipment offers numerous advantages over traditional welding methods. Some key benefits include:
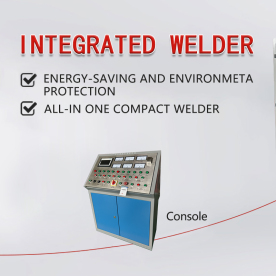
The Importance of High Frequency Welder Equipment in Modern Manufacturing: Enhancing Precision and Efficiency in Welding Processes
2. **Precision:** High frequency welding allows for precise control over the heat generated during the welding process. This precision helps prevent damage to the materials being welded, reducing the risk of defects and rework.
3. **Strong Welds:** The joints produced by high frequency welding are exceptionally strong, often outperforming those made through traditional techniques. This strength is particularly important in applications that demand high structural integrity, such as automotive and aerospace components.

The Importance of High Frequency Welder Equipment in Modern Manufacturing: Enhancing Precision and Efficiency in Welding Processes
5. **Versatility:** The versatility of high frequency welding equipment allows it to be adapted for various materials and applications, making it a valuable tool for manufacturers across multiple sectors.
**Conclusion**
In summary, high frequency welder equipment has become an essential component of modern manufacturing, enabling industries to enhance the precision and efficiency of their welding processes. From automotive to aerospace, the applications are wide-ranging and continually evolving. As technology advances, we can expect to see even more innovative uses of high frequency welding in sectors that demand high-quality, reliable, and efficient production methods. By incorporating high frequency welding into their operations, manufacturers position themselves to meet the challenges of today’s fast-paced market while ensuring the durability and quality of their products.