[Precision-control All-in-one Welding Equipment]Exploring the Advantages and Innovations of Precision-Control All-in-One Welding Equipment for Modern Manufacturing Applications
News 2024-10-17
In the ever-evolving world of manufacturing and fabrication, the demand for high-quality welding solutions is more pressing than ever. Enter the realm of precision-control all-in-one welding equipment, a technological marvel that combines multiple welding processes into a single, cohesive unit. This innovation not only enhances efficiency but also delivers unparalleled accuracy and consistency, meeting the stringent requirements of modern industries.
The Importance of Precision in Welding
Welding is an integral part of many manufacturing processes, serving as the backbone for the assembly of various structures and components. The quality of a weld directly impacts the strength, durability, and overall performance of the final product. Traditional welding methods often require several machines and tools for different weld types—MIG, TIG, Stick, or Flux-Cored welding. This reliance on multiple machines can lead to inconsistencies, increased downtime, and reduced productivity.
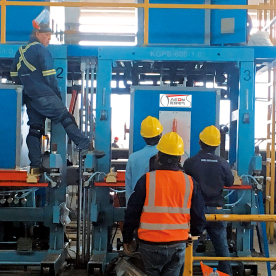
Exploring the Advantages and Innovations of Precision-Control All-in-One Welding Equipment for Modern Manufacturing Applications
Key Features of Precision-Control All-in-One Welding Equipment
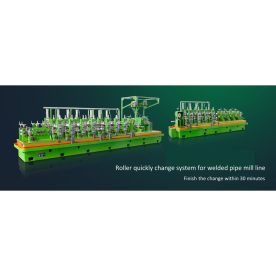
Exploring the Advantages and Innovations of Precision-Control All-in-One Welding Equipment for Modern Manufacturing Applications
2. **Advanced Control Systems**: The heart of precision-control equipment lies in its sophisticated control systems. These systems utilize modern technological advancements, such as digital displays and programmable settings, allowing for precise adjustments to parameters like voltage, amperage, and feed speed. Operators can dial in exact specifications tailored to the materials and weld type, enhancing overall quality and consistency.
3. **Portability and Space Efficiency**: Many manufacturers operate under constraints related to space and equipment handling. All-in-one welding machines are designed with portability in mind. Compact and lightweight, these units can fit into tight workshop spaces and can be easily transported to different job sites, making them an ideal choice for on-the-go operators.

Exploring the Advantages and Innovations of Precision-Control All-in-One Welding Equipment for Modern Manufacturing Applications
5. **Cost-Effectiveness**: While the initial investment in precision-control all-in-one equipment may be higher than purchasing individual machines, the long-term benefits can outweigh the costs. Reduced maintenance needs, lower operational costs, and improved productivity contribute to a quicker return on investment. Furthermore, companies can save on floor space and eliminate the need for multiple operators, thus optimizing their workforce.
The Impact on Modern Manufacturing
As industries continue to adopt automation and advanced manufacturing techniques, precision-control all-in-one welding equipment is becoming an essential tool. Its ability to enhance quality and efficiency resonates within sectors that demand high levels of precision, including automotive manufacturing, aerospace engineering, and structural fabrication.
Additionally, with the growing emphasis on sustainability and waste reduction, these all-in-one systems are designed to minimize spatter and waste, promoting cleaner welding processes. The shift towards greener production methods aligns with global initiatives aimed at minimizing the environmental impact of manufacturing operations.
Conclusion
In conclusion, precision-control all-in-one welding equipment represents a significant advancement in welding technology, offering an array of benefits that make it an indispensable asset for today's manufacturers. Its versatility, advanced control features, and efficiency not only facilitate high-quality welds but also enhance overall manufacturing performance.
As the industry evolves, embracing innovations like precision-control all-in-one welding systems will be crucial for businesses striving to stay competitive, improve production outcomes, and meet the growing demands of the market. Investing in this cutting-edge equipment is not merely a choice—it is a strategic step towards future-proofing manufacturing operations in an increasingly complex landscape.