[Automatic ERW tube mill equipment]An In-Depth Overview of Automatic ERW Tube Mill Equipment: Innovations, Benefits, and Applications in Modern Manufacturing
News 2024-10-16
****In the realm of modern manufacturing, the demand for high-quality steel tubes and pipes has surged, driven by numerous sectors such as construction, automotive, and energy. To meet this growing demand efficiently and effectively, manufacturers have increasingly turned to Automatic Electrical Resistance Welding (ERW) tube mill equipment. This advanced technology not only enhances productivity but also ensures superior product quality. In this article, we will explore the features, innovations, benefits, and applications of Automatic ERW tube mill equipment.
Understanding ERW Tube Mill Equipment
Automatic ERW tube mill equipment is specifically designed for producing high-precision steel tubes and pipes through a continuous manufacturing process. The process involves the manipulation of flat steel coils, which are fed into the mill and subsequently shaped into a tubular form. The edges of the strip are then brought together and welded using high-frequency electrical resistance, producing a strong and seamless tube.
Key Innovations in Automatic ERW Tube Mill Equipment
Recent advancements in technology have significantly transformed the capabilities of ERW tube mills. Some of the most notable innovations include:
1. **Advanced Control Systems**: Incorporating precision control systems, modern tube mills can monitor and adjust multiple parameters in real-time, ensuring consistent quality throughout the manufacturing process. These systems enable the automation of tasks such as welding speed, temperature, and pressure, minimizing human error and improving production efficiency.
2. **High-Quality Welding Techniques**: Automatic ERW tube mills now utilize state-of-the-art welding technologies that enhance joint strength and overall product integrity. Techniques such as induction welding and laser welding are increasingly being integrated into tube mill operations, providing more robust and reliable welding solutions.
3. **Material Versatility**: Today's Automatic ERW tube mill equipment can process a variety of materials, including carbon steel, stainless steel, and alloy steel. This adaptability allows manufacturers to cater to diverse market needs and production requirements.
4. **Eco-Friendly Operations**: With an increasing focus on sustainability, modern tube mills often incorporate energy-efficient designs and processes. These machines are optimized to minimize waste, reduce energy consumption, and limit environmental impact.
Benefits of Using Automatic ERW Tube Mill Equipment
The adoption of Automatic ERW tube mill equipment offers several advantages to manufacturers:
1. **Increased Production Speed**: The automation aspect of these mills significantly boosts production rates. Continuous operation and efficient material handling result in higher output levels compared to manual processes.
2. **Consistent Product Quality**: The integration of advanced control systems ensures that every tube produced meets stringent quality standards. The precision of automated welding and cutting leads to fewer defects and a more uniform product line.
3. **Cost Efficiency**: By reducing labor costs and minimizing material waste, Automatic ERW tube mills offer an appealing return on investment. The efficiency gains translate to lower production costs, allowing manufacturers to remain competitive in today’s market.
4. **Flexibility in Production**: Automatic ERW tube mills can be adjusted quickly to produce different sizes and specifications of tubes. This flexibility is crucial in a market where customization and rapid response to customer demands are increasingly important.
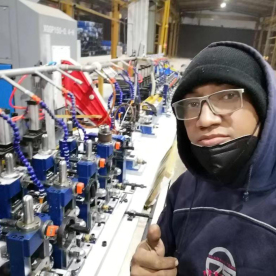
An In-Depth Overview of Automatic ERW Tube Mill Equipment: Innovations, Benefits, and Applications in Modern Manufacturing
The versatility of Automatic ERW tube mill equipment allows it to be used in a wide array of applications across various industries:
1. **Construction Industry**: ERW tubes are extensively used in construction for structural applications, such as scaffolding, railings, and columns.
2. **Automotive Industry**: These tubes play a vital role in manufacturing components like exhaust systems, chassis, and fuel lines, which require strength and reliability.
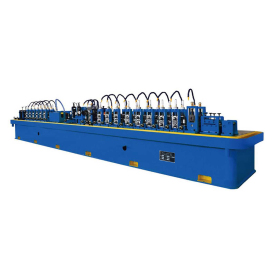
An In-Depth Overview of Automatic ERW Tube Mill Equipment: Innovations, Benefits, and Applications in Modern Manufacturing
4. **Manufacturing and Fabrication**: The versatility of ERW pipes allows them to be integrated into a multitude of manufacturing and fabrication processes, contributing to the creation of various products.
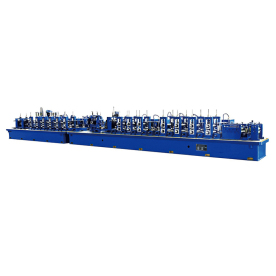
An In-Depth Overview of Automatic ERW Tube Mill Equipment: Innovations, Benefits, and Applications in Modern Manufacturing
Automatic ERW tube mill equipment stands at the forefront of modern manufacturing, combining innovative technologies with exceptional efficiency. As industries continue to evolve, the importance of high-quality, reliable production methods will only increase. Investing in Automatic ERW tube mill equipment prepares manufacturers not only to meet current demands but also to embrace future challenges in an ever-changing landscape. The blend of speed, quality, and sustainability offered by these machines is set to drive the next generation of tube manufacturing.