[Customized ERW tube mill solutions]Discovering the Benefits of Customized ERW Tube Mill Solutions for Enhanced Production Efficiency and Quality in Manufacturing
News 2024-10-13
****In the world of manufacturing, precision and efficiency are paramount. Among the key components in achieving these goals are Electric Resistance Welded (ERW) tubes, essential in various applications ranging from construction and automotive to energy and infrastructure. To meet the ever-evolving demands of these industries, manufacturers are increasingly turning to customized ERW tube mill solutions. This article explores the significance of these tailored systems, detailing their advantages, components, and contribution to operational excellence.
Understanding ERW Tube Mills
ERW tube mills utilize a process that involves rolling metal sheets into tubes and welding their seams with electric resistance heating. This efficient method enables the production of high-quality steel tubes with specific mechanical properties suitable for diverse applications. The versatility of ERW tube mills lies in their ability to produce a wide range of sizes, thicknesses, and metallurgical properties, making them indispensable in modern manufacturing.
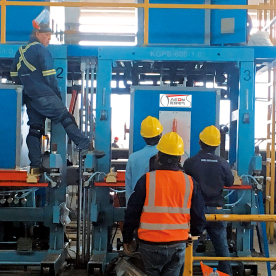
Discovering the Benefits of Customized ERW Tube Mill Solutions for Enhanced Production Efficiency and Quality in Manufacturing
As market demands become more specialized, the need for customized ERW tube mill solutions has intensified. A one-size-fits-all approach is no longer sufficient to meet the unique requirements of various sectors. Tailored designs allow manufacturers to optimize their production processes, reduce waste, and enhance product quality.
Key Benefits of Customized ERW Tube Mill Solutions
1. **Enhanced Production Efficiency**: Customized tube mills can be designed to fit specific production volumes and speeds, maximizing throughput. With bespoke configurations, manufacturers can streamline processes, minimizing downtime and improving operational efficiency. This tailored approach reduces the time needed to switch between product types, which is especially beneficial for companies that handle a variety of orders.
2. **Precision and Quality Control**: Custom solutions incorporate advanced technologies and automation systems that ensure precise control over the welding process. This leads to improved weld quality, reduced defects, and enhanced mechanical properties of the finished tubes. By minimizing variability in production, manufacturers can maintain consistent quality standards that meet or exceed regulatory requirements.
3. **Flexibility in Design**: Customized ERW tube mills are adaptable to produce various tube sizes and shapes, including round, square, and rectangular sections. Manufacturers can adjust to the changing market needs without investing in completely new machinery. This flexibility is essential for companies looking to diversify their product offerings or respond rapidly to market trends.
4. **Cost-Effective Solutions**: While the initial investment in customized equipment may seem substantial, the long-term savings often outweigh the costs. Custom ERW tube mills lead to decreased scrap rates and minimize the need for secondary operations, thus reducing overall production costs. Furthermore, enhanced efficiency can boost profitability by allowing for increased production volume without a proportional increase in operational expenses.
5. **Sustainability and Reduced Waste**: Custom solutions can be designed with sustainability in mind. By optimizing the production process and minimizing waste, manufacturers can significantly reduce their environmental impact. Incorporating energy-efficient technologies not only assists in meeting regulations but can also lead to cost savings in energy consumption.
Components of Customized ERW Tube Mill Solutions
Customized ERW tube mills typically include several key components that can be individually tailored:
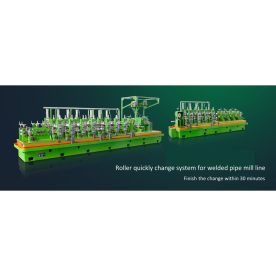
Discovering the Benefits of Customized ERW Tube Mill Solutions for Enhanced Production Efficiency and Quality in Manufacturing
- **Forming and Sizing Equipment**: Custom tooling can be used to ensure the required dimensional and geometric accuracy of the tubes produced.

Discovering the Benefits of Customized ERW Tube Mill Solutions for Enhanced Production Efficiency and Quality in Manufacturing
- **Automation and Control Systems**: state-of-the-art automation can be incorporated to monitor and optimize production in real time, enhancing overall efficiency.
Conclusion
Customized ERW tube mill solutions represent a crucial advancement in manufacturing technology, providing companies with the ability to produce high-quality, efficient, and flexible tube products that meet market demands. By investing in tailored solutions, manufacturers can achieve operational excellence and maintain competitiveness in the ever-changing landscape of industry. As the demand for specialized tube products continues to grow, the shift towards customization in fabrication processes is an essential step toward a sustainable and productive manufacturing future.