[High-precision tube making machine ]Exploring the Innovations and Advancements in High-Precision Tube Making Machines for Modern Manufacturing
News 2024-10-13
In today's highly competitive manufacturing landscape, efficiency and precision are paramount. Industries ranging from automotive to aerospace are heavily reliant on high-quality components, and tube making is no exception. The rise of high-precision tube making machines has revolutionized the way tubes are produced, ensuring that they meet the rigorous standards required for advanced applications. This article delves into the significance, capabilities, and future trends of high-precision tube making machines.
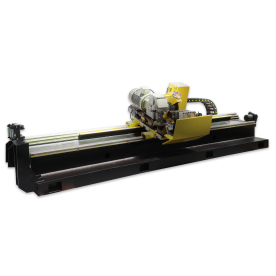
Exploring the Innovations and Advancements in High-Precision Tube Making Machines for Modern Manufacturing
One of the most notable advantages of high-precision tube making machines is their ability to handle a wide range of materials. From stainless steel and aluminum to specialized alloys, these machines are capable of producing tubes that meet specific mechanical properties and corrosion resistance requirements. The versatility of these machines allows manufacturers to target diverse markets and applications, which is especially valuable in an era where customization is increasingly expected.
Moreover, the automation features integrated into modern high-precision tube making machines significantly enhance productivity and reduce human error. Automated feeders, programmable controllers, and intelligent monitoring systems enable manufacturers to achieve higher output rates while maintaining quality standards. These machines can be set up to operate with minimal intervention, allowing skilled workers to focus on other critical tasks, thereby optimizing overall operational efficiency.
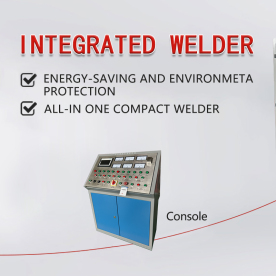
Exploring the Innovations and Advancements in High-Precision Tube Making Machines for Modern Manufacturing
As the industry grows, sustainability becomes an increasingly important factor in manufacturing processes. High-precision tube making machines have also evolved to accommodate eco-friendly practices. By optimizing material usage and minimizing waste through precise cutting and bending, these machines contribute positively to a manufacturer's sustainability goals. Furthermore, many manufacturers are focusing on developing energy-efficient machines that require less power to operate without compromising performance.
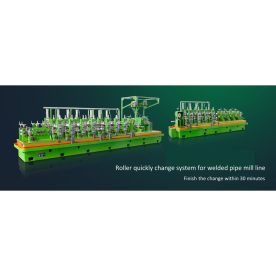
Exploring the Innovations and Advancements in High-Precision Tube Making Machines for Modern Manufacturing
Additionally, as industries demand more complex tube designs and configurations, manufacturers will continue to push the boundaries of what high-precision tube making machines can achieve. The advent of 3D printing technologies may also complement traditional tube manufacturing methods, offering new avenues for creating complex geometries that were previously deemed impractical.
In conclusion, high-precision tube making machines are vital to modern manufacturing, playing a crucial role in producing high-quality tubes needed across various industries. Their precision, versatility, automation capabilities, and commitment to sustainability make them indispensable tools in the quest for excellence in production. As technology advances and market demands shift, the evolution of high-precision tube making machines will undoubtedly continue, shaping the future of manufacturing and opening new doors for innovation and growth.