[Automatic ERW tube mill equipment]Unlocking Efficiency and Precision in Metal Fabrication: The Role of Automatic ERW Tube Mill Equipment in Modern Manufacturing Processes
News 2024-10-10
In the ever-evolving landscape of metal fabrication and manufacturing, precision and efficiency are paramount. As industries continue to demand higher quality, lower costs, and faster turnaround times, the spotlight has turned to automatic equipment that can streamline operations. One such innovation that has transformed the industry is the Automatic Electric Resistance Welded (ERW) tube mill equipment. This technology represents a significant advance in the production of high-quality steel tubes and pipes, serving various sectors, including construction, automotive, and energy.
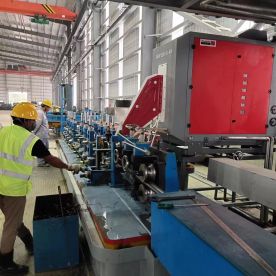
Unlocking Efficiency and Precision in Metal Fabrication: The Role of Automatic ERW Tube Mill Equipment in Modern Manufacturing Processes
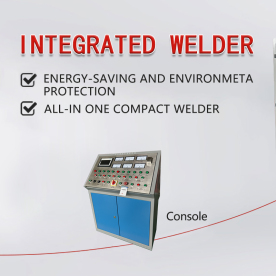
Unlocking Efficiency and Precision in Metal Fabrication: The Role of Automatic ERW Tube Mill Equipment in Modern Manufacturing Processes
Moreover, the automatic nature of these systems ensures high levels of consistency and quality control across production runs. Advanced quality inspection mechanisms, such as in-line ultrasonic testing and laser measurement systems, monitor the dimensions and weld integrity in real-time. This capability significantly reduces the risk of defects, ensuring that the final products meet industry standards and customer expectations. As a result, manufacturers can build a reputation for reliability, which is crucial for securing contracts and retaining clients in competitive industries.
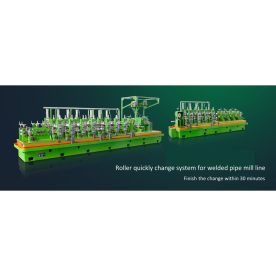
Unlocking Efficiency and Precision in Metal Fabrication: The Role of Automatic ERW Tube Mill Equipment in Modern Manufacturing Processes
Another aspect that makes Automatic ERW tube mill equipment an attractive investment is its versatility. These mills can produce a wide range of tube sizes and shapes, accommodating various applications. This flexibility allows manufacturers to diversify their product offerings and respond swiftly to changes in market demand. Industries such as oil and gas rely heavily on high-quality tubes and pipes, and a mill capable of producing a range of dimensions can cater to these diverse requirements without the need for significant equipment changes.
The implementation of automatic ERW tube mills is not without challenges, however. Initial investment costs can be substantial, which may deter smaller manufacturers from upgrading their equipment. Additionally, the need for skilled technicians to operate and maintain these advanced systems cannot be overlooked. As technology progresses, ongoing training and development of the workforce will be needed to harness the full potential of these automated systems and adjust to innovations in the industry.
In conclusion, Automatic ERW tube mill equipment stands at the forefront of modern manufacturing, driving advancements in efficiency, quality, and sustainability. Its ability to adapt to market demands and provide consistent output makes it an indispensable asset for manufacturers in various sectors. As industries continue to evolve and face new challenges, investing in such technology can provide manufacturers with the edge they need to thrive in a competitive environment. The future of tube and pipe production will undoubtedly be shaped by the capabilities and innovations brought forth by automatic ERW tube mill equipment.