[Pipe mill production line with welding and cutting functions]Innovative Pipe Mill Production Line: Revolutionizing Manufacturing with Advanced Welding and Cutting Functions for Enhanced Efficiency and Quality
News 2024-10-10
The growth of the manufacturing industry has spurred the need for efficient and effective production methods, particularly in the fabrication of pipes used across various sectors, including construction, oil and gas, and water supply. One of the most significant advancements in this field is the development of modern pipe mill production lines that incorporate advanced welding and cutting functions. These lines not only enhance productivity but also ensure the quality and precision of the final products.
Overview of Pipe Mill Production Lines
A pipe mill production line is a sophisticated system designed to manufacture pipes from raw materials such as steel or other alloys. The line typically consists of a series of processes, including casting, forming, welding, and cutting, which work in a harmonious sequence to transform raw materials into finished pipes ready for distribution. The incorporation of welding and cutting functions is critical in this process, as these operations determine the strength, durability, and dimensional accuracy of the pipes produced.
Importance of Welding Functions in Pipe Manufacturing
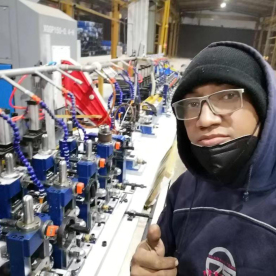
Innovative Pipe Mill Production Line: Revolutionizing Manufacturing with Advanced Welding and Cutting Functions for Enhanced Efficiency and Quality
Automated welding technology offers several advantages:
1. **Consistency and Quality**: Automated welding ensures uniformity in the welding process, minimizing the risk of human error. This leads to pipes with consistent quality, which is crucial for meeting industry standards and customer expectations.
2. **Increased Production Speed**: The automation of welding allows for rapid production cycles. Traditional methods may require manual intervention, which can slow down the process. However, automated systems can operate at high speeds, significantly increasing the output of the pipe mill.

Innovative Pipe Mill Production Line: Revolutionizing Manufacturing with Advanced Welding and Cutting Functions for Enhanced Efficiency and Quality
4. **Enhanced Safety**: Automation reduces the need for manual intervention in potentially hazardous welding environments. This not only protects workers but also reduces the likelihood of production errors resulting from fatigue or distraction.
Cutting Functions: Precision and Efficiency

Innovative Pipe Mill Production Line: Revolutionizing Manufacturing with Advanced Welding and Cutting Functions for Enhanced Efficiency and Quality
1. **Precision**: Automated cutting machines can achieve remarkably accurate cuts, ensuring that each pipe meets specified dimensions. This precision is vital in applications where even minor deviations can affect the performance and integrity of the pipe.
2. **Speed**: Similar to welding, automated cutting processes significantly speed up the production timeline. For manufacturers, this means shorter lead times and increased ability to meet client demands.
3. **Versatility**: Advanced cutting technologies are versatile and can handle a variety of pipe sizes and materials. This flexibility allows manufacturers to produce a wider range of products, catering to various industry requirements.
4. **Cost-Effectiveness**: By minimizing material waste and reducing labor costs through automation, advanced cutting functions contribute to the overall cost-effectiveness of the pipe production line.
Conclusion
As the demand for high-quality pipes continues to rise, the implementation of innovative pipe mill production lines with advanced welding and cutting functions becomes increasingly critical. These state-of-the-art technologies not only streamline the manufacturing process but also enhance the final product's quality, safety, and sustainability. Moving forward, manufacturers that invest in these modern production lines will likely gain a competitive edge, allowing them to better serve their customers while maintaining profitability in an ever-evolving industry. Embracing these advancements is essential for staying ahead in the competitive landscape of pipe manufacturing.