[Precision Tube making equipment]Unlocking the Potential of High-Quality Manufacturing: The Role of Precision Tube Making Equipment in Modern Industries
News 2024-10-9
In an era marked by rapid industrialization and technological advancements, the demand for precision-engineered products has reached unprecedented heights. Among the various manufacturing processes, the production of precision tubes stands out due to its critical role in various applications, ranging from automotive and aerospace to medical and electronics sectors. A crucial element in this process is the precision tube making equipment, which has evolved significantly over the years, providing manufacturers with the tools required to meet stringent quality standards and deliver high-performance products.
Precision tube making equipment encompasses a wide range of machinery designed to create tubes with exact dimensions, tolerances, and surface finishes. This equipment includes tube mills, bending machines, cutting systems, and inspection tools, all of which contribute to the fabrication of tubes utilized in diverse applications. One of the primary advantages of using precision tube manufacturing technology is its ability to produce tubes at scale without compromising quality. This scalability is particularly important in industries where large quantities of tubes are needed to fulfill production demands.
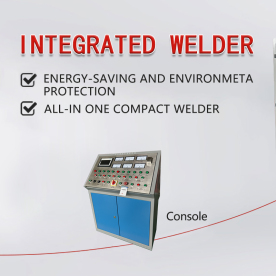
Unlocking the Potential of High-Quality Manufacturing: The Role of Precision Tube Making Equipment in Modern Industries
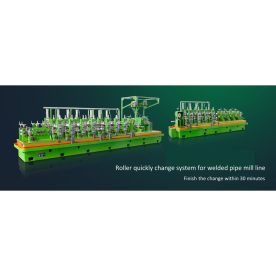
Unlocking the Potential of High-Quality Manufacturing: The Role of Precision Tube Making Equipment in Modern Industries

Unlocking the Potential of High-Quality Manufacturing: The Role of Precision Tube Making Equipment in Modern Industries
Quality control is another area where precision tube making equipment shines. Advanced inspection tools such as laser measurement systems and ultrasonic tests ensure that each tube meets the required specifications. This proactive approach to quality management is crucial in maintaining the reliability and performance of the tubes, particularly in industries where failure is not an option. The end result is a commitment to producing tubes that not only meet but exceed industry standards.
Furthermore, the integration of Industry 4.0 technology, including IoT devices and data analytics, has revolutionized the capabilities of precision tube making equipment. These advancements allow manufacturers to monitor production processes in real-time, optimize workflows, and reduce downtime. Predictive maintenance tools can identify potential equipment failures before they occur, ensuring continued operations and significant cost savings over time.
The impact of precision tube making equipment extends beyond manufacturing efficiency. By producing high-quality tubes that enhance performance in applications, manufacturers also contribute to sustainability efforts. Products made from precision tubes often require less material without sacrificing strength and are designed for energy efficiency, aligning with the global push toward environmental responsibility.
In conclusion, precision tube making equipment stands as a cornerstone of modern manufacturing, facilitating the production of high-quality tubes that are integral to various industries. The continuous evolution of this equipment, driven by technological advancements and growing market demands, ensures that manufacturers can meet the challenges of today’s dynamic industrial landscape. Ultimately, the investment in precision tube making equipment is not merely an investment in machinery but an investment in quality, efficiency, and innovation that defines the future of manufacturing.