[Solid state high frequency welder machine]Understanding the Advantages and Applications of Solid State High Frequency Welder Machines in Modern Manufacturing Processes
News 2024-10-9
In the evolving landscape of manufacturing technology, the solid state high frequency welder machine stands out as a pivotal innovation. As industries prioritize efficiency, precision, and reliability, these machines offer a compelling solution for various welding needs. This article delves into the operational principles, advantages, and applications of solid state high frequency welders, showcasing why they have become essential in various industrial applications.
What Is a Solid State High Frequency Welder Machine?
A solid state high frequency welder machine utilizes solid state electronics to produce high-frequency electrical currents. This technology allows for the welding of metals and thermoplastics through a process known as dielectric heating, effectively softening and joining materials through controlled application of heat. Unlike traditional welding methods, which often rely on bulky transformers and extensive equipment setups, solid state welders are more compact, lightweight, and energy-efficient.
Operational Principles
The core of a solid state high frequency welder is its ability to convert electrical energy into a high-frequency current. This current flows through the workpieces, generating heat due to resistance. In most cases, the frequency of the current ranges from 27.12 MHz to 40.68 MHz, allowing for rapid heating of the materials. The innovative design of these welders minimizes energy loss, ensuring a high degree of efficiency.
The solid state design means fewer mechanical components and greater reliability. This translates into reduced maintenance needs, lower operational costs, and longer equipment lifespan. They are particularly suited for high-speed welding applications, where precision and speed are paramount for production efficiency.
Advantages of Solid State High Frequency Welding
1. **Energy Efficiency**: Solid state high frequency welders consume significantly less energy compared to traditional induction or resistance welding methods. Their design allows for efficient energy usage, resulting in lower utility costs for manufacturers.
2. **Precision**: These machines provide high levels of control over the welding process. With the ability to fine-tune frequency settings, operators can adjust parameters to suit specific materials and thicknesses, leading to superior weld quality and reduced risk of defects.
3. **Compact Design**: The solid state design is inherently compact, enabling more efficient use of manufacturing floor space. This is particularly beneficial for facilities with space constraints, allowing them to integrate advanced welding technology without requiring extensive layout changes.
4. **Versatility**: Solid state high frequency welders can work with diverse materials, including different metals and thermoplastics. This versatility makes them invaluable in industries ranging from automotive and aerospace to packaging and electronics.
5. **Reduced Maintenance**: With fewer moving parts and a more straightforward design, solid state welders require significantly less maintenance than their traditional counterparts. This not only lowers operational costs but also minimizes downtime, enhancing overall productivity.
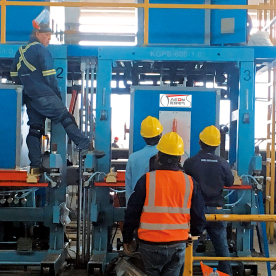
Understanding the Advantages and Applications of Solid State High Frequency Welder Machines in Modern Manufacturing Processes
The applications of solid state high frequency welder machines are vast and varied:
- **Automotive Manufacturing**: These welders are extensively used for assembling components like radiators, fuel tanks, and electrical harnesses. Their ability to create strong, reliable welds is crucial for the safety and performance of automotive products.
- **Aerospace Engineering**: The aerospace industry demands the highest standards of precision and quality. Solid state welders help in fabricating lightweight structures that meet stringent regulatory requirements while maintaining structural integrity.
- **Packaging Industry**: In the packaging sector, these machines are employed for welding flexible packaging materials, ensuring airtight seals that preserve product freshness and prolong shelf life.
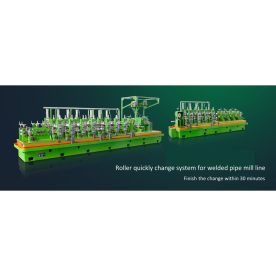
Understanding the Advantages and Applications of Solid State High Frequency Welder Machines in Modern Manufacturing Processes

Understanding the Advantages and Applications of Solid State High Frequency Welder Machines in Modern Manufacturing Processes
Conclusion
As industries continue to embrace automation and technological advancements, solid state high frequency welder machines are at the forefront of driving efficiency and quality. Their energy-saving capabilities, precision, and versatility make them an indispensable tool for manufacturers across various sectors. With the growing demand for advanced manufacturing solutions, investing in solid state technology represents not just an opportunity for enhanced productivity but also a commitment to quality and sustainability in production processes.