[Solid state high frequency welder]The Advancements and Applications of Solid State High Frequency Welders in Modern Manufacturing Processes
News 2024-10-9
In the ever-evolving world of manufacturing, the need for efficient, reliable, and precise welding technologies has never been greater. Among various welding methods, solid state high frequency welders have emerged as a game-changer, revolutionizing the way materials are joined. These sophisticated machines use high-frequency electrical currents to create welds, and they present numerous benefits over traditional welding methods. This article delves into the advancements and applications of solid state high frequency welders in modern manufacturing processes.
Solid state high frequency welders operate by utilizing high-frequency electric currents that generate heat through resistance in the material being welded. Unlike traditional welding methods, which may employ gas or arc processes, solid state technology allows for a more controlled approach to welding, resulting in cleaner, stronger, and more precise welds. The core components of a solid state welder include power supplies, inverters, and control systems that manage the frequency and amplitude of the current, ensuring optimal welding conditions.
One of the most significant advancements in solid state high frequency welding technology is the implementation of digital controls and sensors. These advancements allow operators to monitor and adjust welding parameters in real-time, ensuring that every weld is consistent and of the highest quality. Additionally, modern machines are often equipped with user-friendly interfaces, making it easier to program different welding specifications for various materials and applications. These technological enhancements have significantly increased production efficiency, reduced scrap rates, and improved the overall quality of the welds.
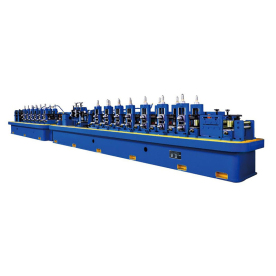
The Advancements and Applications of Solid State High Frequency Welders in Modern Manufacturing Processes
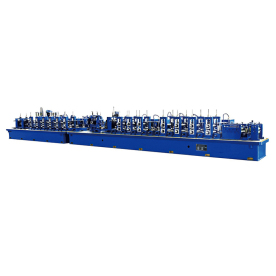
The Advancements and Applications of Solid State High Frequency Welders in Modern Manufacturing Processes
Safety is another essential factor where solid state high frequency welders excel. The controlled nature of high-frequency welding reduces the risk of burn injuries and fire hazards, making it a safer alternative to traditional welding methods. Additionally, the closed-loop systems in modern machines often include safety features that protect operators from exposure to harmful fumes and radiation, further enhancing workplace safety.
The application of solid state high frequency welders is not limited to high-volume production environments. Smaller fabricators and custom workshops are increasingly adopting this technology as well. The portability and user-friendly design of newer solid state welders make them suitable for various applications, such as repair work and crafting specialized components. As these machines continue to evolve, we may see even greater adaptability to niche markets and specialized welding processes.
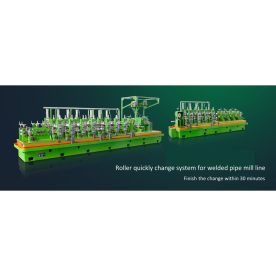