[Solid state HF welder]Exploring the Innovative Advancements and Applications of Solid State HF Welders in Modern Manufacturing Processes
News 2024-10-8
The welding industry has undergone a significant transformation over the past few decades, and one of the most noteworthy advancements contributing to this change is the solid state high-frequency (HF) welder. This technology has revolutionized the way welding is performed, offering enhanced precision, efficiency, and reliability in various manufacturing applications. This article explores the innovative advancements of solid state HF welders, their mechanics, benefits, and applications, ultimately illustrating their pivotal role in modern manufacturing.
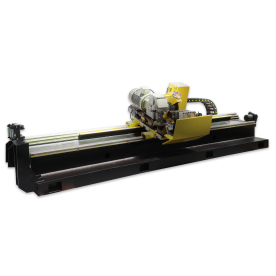
Exploring the Innovative Advancements and Applications of Solid State HF Welders in Modern Manufacturing Processes
Solid state HF welders are a modern engineering solution that employs high-frequency currents to achieve welds with minimal distortion and impressive accuracy. Unlike traditional welders, which rely on vacuum tubes for power amplification, solid state devices utilize semiconductor technology to generate high-frequency currents. This innovation not only improves the consistency and control of the welding process but also significantly enhances energy efficiency.
The solid state HF welder operates by converting electrical energy into high-frequency, high-voltage electric pulses that are delivered to the welding electrodes. The process starts with the material preparation, where surfaces are cleaned and positioned accurately. When the electric pulses contact the materials, they generate sufficient thermal energy to melt and fuse them together. The benefits of this type of welding are particularly evident in applications involving thinner materials and complex geometries, where traditional welding methods may result in warping or uneven joints.
**Advantages of Solid State HF Welders**
One of the primary advantages of solid state HF welders is their superior energy efficiency. The conversion process used in solid state technology minimizes energy losses, resulting in reduced operational costs while maintaining the quality of the welds. Moreover, these machines exhibit excellent repeatability, ensuring that every weld produced meets strict quality standards.
Another significant benefit is the ability to weld different types of materials, including metals and plastics. This versatility opens up a wide array of potential applications across various industries. Furthermore, solid state technology allows for finer control of the welding parameters, including frequency, power output, and pressure, leading to more tailored and optimized welds based on material type and thickness.
Additionally, solid state HF welders tend to be more compact and lightweight compared to their traditional counterparts, making them easier to integrate into existing production setups. The reduced size also allows for greater mobility, enabling operators to perform welding tasks in various locations within a manufacturing facility.
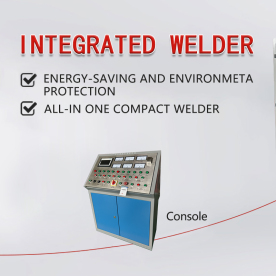
Exploring the Innovative Advancements and Applications of Solid State HF Welders in Modern Manufacturing Processes
The applications of solid state HF welders span a broad spectrum of industries, including automotive, aerospace, electronics, and textiles. In the automotive sector, these welders are utilized for welding wires in harnesses, which are crucial for connecting different electronic components within vehicles. The precision and efficiency of solid state HF welders play a key role in ensuring the reliability and longevity of these electrical connections.
In aerospace manufacturing, where high standards of safety and reliability are mandatory, solid state HF welders are employed for joining lightweight materials and components used in aircraft. The technology's ability to produce strong, yet lightweight, welds supports the overall performance and fuel efficiency of modern aircraft designs.
The electronics industry also benefits from solid state HF welders, particularly in the manufacturing of circuit boards and other electronic components. These welders facilitate the connection of fine wires and intricate components with unmatched precision, enhancing the quality and functionality of the final products.
In the textile industry, solid state HF welders are used for fabric welding. This application has gained traction for creating strong seams in synthetic fabrics used in various products such as outdoor gear, tarpaulins, and automotive interiors. The technology offers advantages over traditional sewing methods by creating seamless joints that are more resistant to water and stress.
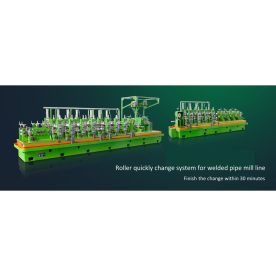
Exploring the Innovative Advancements and Applications of Solid State HF Welders in Modern Manufacturing Processes
Solid state HF welders represent a remarkable step forward in welding technology, combining efficiency, precision, and versatility in one powerful package. As manufacturers seek to optimize production processes while maintaining high-quality standards, the adoption of solid state HF welders is poised to become even more prevalent. By enabling quick, reliable, and high-quality welds across a range of materials and applications, solid state HF welders play a critical role in shaping the future of modern manufacturing. As technology continues to evolve, these innovative welders are likely to further enhance operational efficiency and product quality in an ever-competitive marketplace.