[Automatic high frequency welder]Exploring the Advantages and Applications of Automatic High Frequency Welders in Modern Manufacturing Processes
News 2024-10-7
In the fast-paced world of manufacturing, efficiency and precision are paramount. Among the various welding technologies available, the Automatic High Frequency Welder stands out as a game changer, offering numerous benefits that cater to a wide range of industrial applications. This article delves deeply into what Automatic High Frequency Welders are, their mechanisms, benefits, and the integral role they play in enhancing the productivity of modern manufacturing environments.
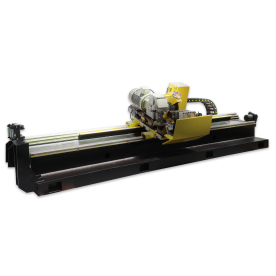
Exploring the Advantages and Applications of Automatic High Frequency Welders in Modern Manufacturing Processes
In addition to speed, the precision of Automatic High Frequency Welders is another notable attribute. The welder can be programmed to deliver specific levels of heat and pressure, ensuring consistent and high-quality welds. This level of control is especially crucial in industries that require stringent quality standards, such as aerospace, automotive, and medical equipment manufacturing. The ability to achieve strong, consistent welds not only reduces material wastage but also minimizes the likelihood of defects that could result in costly rework or fines.
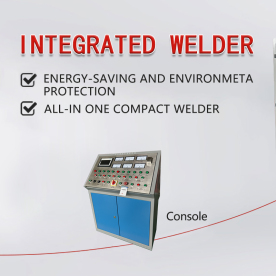
Exploring the Advantages and Applications of Automatic High Frequency Welders in Modern Manufacturing Processes
Applying Automatic High Frequency Welders across multiple sectors is another factor contributing to their popularity. They are widely utilized in industries such as pipe and tube manufacturing, wire bonding, and automotive parts assembly. For instance, in the automotive sector, they aid in the fabrication of exhaust systems, fuel lines, and other critical components, where durability and high performance are essential. The electrical industry utilizes them for producing electrical cables and connections, showcasing the versatility of this technology.

Exploring the Advantages and Applications of Automatic High Frequency Welders in Modern Manufacturing Processes
Moreover, as sustainability becomes a primary focus in the manufacturing field, the reduced waste associated with high-frequency welding makes these welders an attractive option. The precision and efficiency of Automatic High Frequency Welders allow manufacturers to minimize offcuts and scrap, contributing to more sustainable manufacturing processes. This focus on waste minimization aligns well with the growing need for industries to adopt more eco-friendly practices.
The ease of integration into automated production lines is another factor that makes Automatic High Frequency Welders appealing to manufacturers. With the rise of Industry 4.0, the ability to incorporate advanced welding technologies into automated systems has become increasingly important. These welders can seamlessly connect with robotics and automated feeding systems, creating a streamlined manufacturing workflow. This interconnectedness allows businesses to optimize operations, reduce labor costs, and improve safety by minimizing human intervention in potentially hazardous welding environments.
In conclusion, the Automatic High Frequency Welder represents a significant advancement in welding technology, offering numerous benefits that enhance productivity, quality, and sustainability. As industries continue to evolve and require innovative solutions for their manufacturing processes, the role of Automatic High Frequency Welders is likely to expand further. Embracing this technology equips businesses with the necessary tools to remain competitive in an ever-changing landscape, proving that investing in automatic high-frequency welding solutions is not just an option, but a necessity for modern manufacturing success.